What Are Monolithic Refractory Products?
- keruirefra
- 2024年9月4日
- 讀畢需時 5 分鐘
Monolithic refractory products are essential components in industries requiring high-temperature operations, such as metallurgy, cement, and glass manufacturing. Unlike traditional refractory bricks, which are pre-formed and assembled, monolithic refractories are installed as a single cohesive mass. This article delves into the various types of monolithic refractories, their applications, and their manufacturing processes.
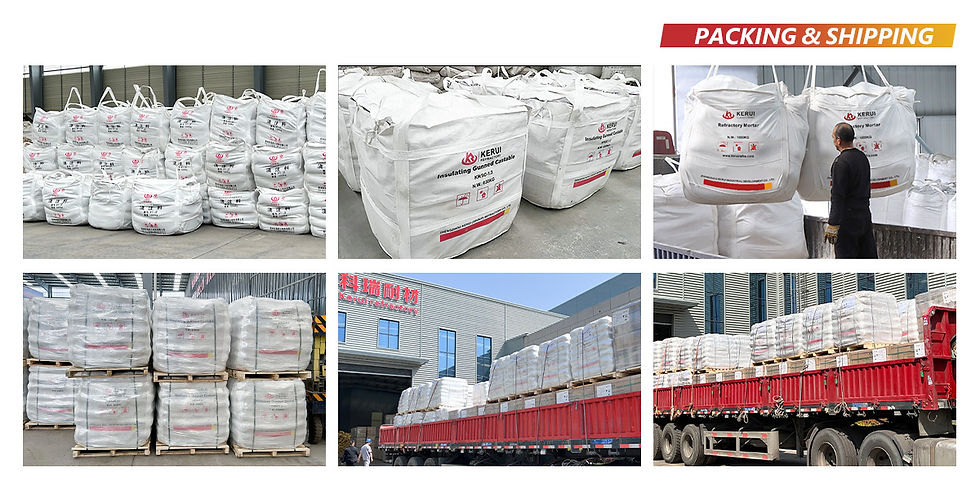
Types of Monolithic Refractory Products
Monolithic castable refractory can be broadly classified into several types based on their composition and the specific conditions they are designed to withstand. The primary categories include:
1. Castables
Castable refractories are designed to be mixed with water and poured or cast into place. They set and harden to form a durable, high-temperature-resistant lining. Castables are further divided into:
Standard Castables: Suitable for general applications with moderate thermal and mechanical stresses.
High-Alumina Castables: Contain a higher proportion of alumina, offering better resistance to abrasion and thermal shock.
Low-Cement Castables: Have reduced amounts of cement, enhancing their performance at high temperatures and providing better resistance to slag and metal attack.
Ultra-Low Cement Castables: Contain minimal amounts of cement, leading to improved high-temperature properties and resistance to corrosion and thermal shock.
2. Gunning Mixes
Gunning mixes are dry refractory mixtures that are applied by a gunning machine. They are projected onto surfaces at high velocity, forming a dense, cohesive layer. This method is particularly useful for repairing and refurbishing refractory linings in situ. Gunning mixes are characterized by:
Wet Gunning Mixes: Require water addition and are applied using a wet gunning machine.
Dry Gunning Mixes: Applied without water, relying on moisture added at the application site.
3. Rammed Masses
Rammed masses are refractories that are compacted and rammed into place. They are commonly used for constructing refractory linings in areas subjected to extreme wear and thermal shock. They are characterized by:
Dense Rammed Masses: High density and strength, suitable for high-impact areas.
Insulating Rammed Masses: Lower density, providing thermal insulation and energy efficiency. Normally, the alumina refractory cement is mixed with ramming mass.
4. Plastics
Refractory plastics are pliable materials that can be shaped and molded by hand or with simple tools. Once placed, they harden into a durable, heat-resistant material. They are used for:
Lining Furnace Walls: Ideal for intricate shapes and repair work.
Patch Repair: Effective for quick repairs of damaged areas.
5. Mortars
Mortars are used to bond refractory bricks or tiles. They can also be applied to small gaps or joints in refractory linings. Types of mortars include:
Acid-Resistant Mortars: Designed to resist acidic slags and gases.
Basic Mortars: Suitable for alkaline environments, such as those found in steelmaking.
6. Self-Flowing Castables
Self-flowing castables are designed to flow easily into molds and self-level, minimizing the need for vibration or tamping. They are particularly useful for complex shapes and intricate linings.
Applications of Monolithic Refractory Products
Monolithic refractories are used in various high-temperature applications where durability, thermal shock resistance, and chemical resistance are critical. Some common applications include:
1. Metallurgical Industry
In the metallurgical industry, monolithic refractories are used in:
Blast Furnaces: To line the furnace and withstand the intense heat and corrosive slag.
Electric Arc Furnaces: Where high thermal and mechanical stresses are encountered.
Steel Ladles: For their ability to withstand molten metal and slag.
2. Cement Industry
In cement kilns, monolithic refractories are employed to:
Line the Kiln Interior: Protecting against extreme temperatures and abrasive materials.
Repair Kiln Shells: Providing a seamless lining that can be repaired quickly.
3. Glass Industry
Monolithic refractories in the glass industry are used to:
Lining Glass Melting Furnaces: Withstand the high temperatures and corrosive nature of molten glass.
Constructing Forehearths: Where precise temperature control and resistance to thermal shock are required.
4. Petrochemical Industry
Monolithic refractories are critical in:
Hydrocrackers and Reformers: To withstand high temperatures and chemical reactions.
Cracking Units: Where resistance to thermal shock and chemical attack is essential.
5. Power Generation
In power generation, particularly in coal-fired and biomass power plants, monolithic refractories are used for:
Boiler Linings: To resist high temperatures and corrosive ash deposits.
Furnace Linings: Ensuring efficient and safe operation of combustion chambers.
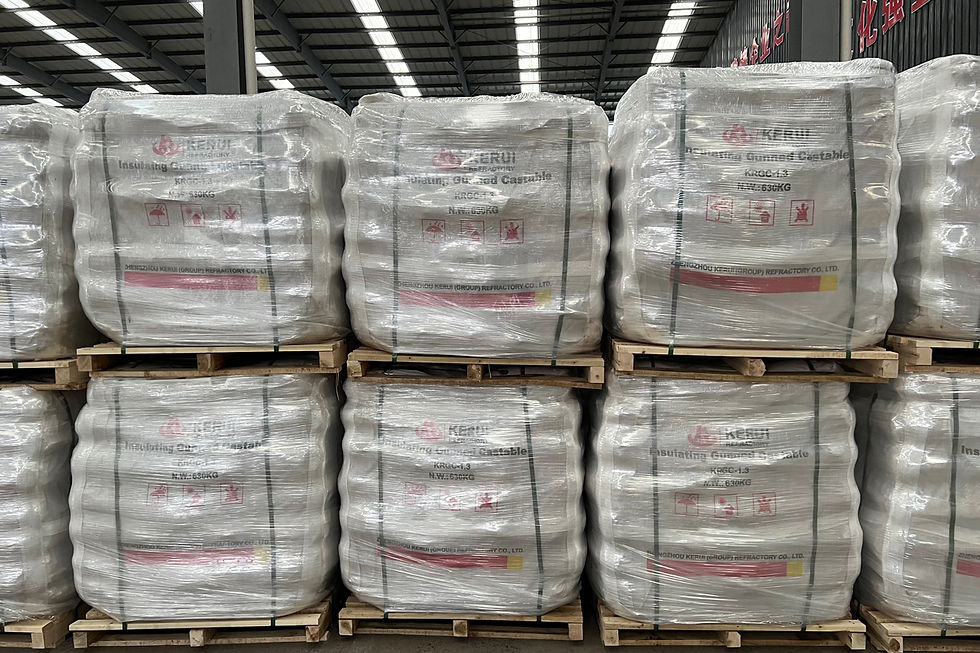
Manufacturing Processes of Monolithic Refractory Products
The manufacturing of monolithic refractory products involves several key steps, each tailored to the type of refractory being produced. The general process includes:
1. Raw Material Selection and Preparation
The quality of monolithic refractories depends on the selection and preparation of raw materials. Common raw materials include:
Alumina: Provides high-temperature stability and resistance to corrosion.
Silica: Offers good thermal shock resistance and strength.
Magnesia: Known for its high melting point and basic slag resistance.
These materials are finely ground and mixed to achieve the desired properties.
2. Mixing
The raw materials are mixed with binders and other additives. The choice of binder (such as cement, calcium aluminate, or phosphates) and additives (like plasticizers and dispersants) depends on the specific type of refractory product being manufactured. The mixing process ensures a homogeneous blend of materials.
3. Forming
Depending on the type of product, the forming process varies:
Casting: For castables, the mixed material is poured into molds and allowed to set.
Gunning: Dry gunning mixes are projected onto surfaces using high-velocity air or mechanical equipment.
Ramming: Rammed masses are compacted into place manually or using specialized equipment.
Plastic Formation: Refractory plastics are shaped by hand or with simple tools.
4. Drying and Curing
After forming, the products undergo drying and curing processes to achieve their final strength. This may involve:
Air Drying: Allowing the product to dry at ambient temperatures.
Heat Curing: Gradually heating the product in kilns or ovens to drive off moisture and enhance strength.
5. Firing
For some types of monolithic refractories, especially those containing high levels of cement or clay, firing at high temperatures may be necessary to achieve the desired properties. Firing involves heating the product in a kiln to develop the final structure and enhance its performance.
6. Quality Control
Throughout the manufacturing process, rigorous quality control measures are implemented to ensure the final product meets the required specifications. This includes testing for physical properties such as strength, thermal shock resistance, and chemical stability.
Conclusion
Monolithic refractory products play a crucial role in high-temperature industries by providing durable, reliable, and efficient solutions for various demanding applications. Their versatility in terms of types, applications, and manufacturing processes makes them indispensable for modern industrial operations. Understanding the different types of monolithic refractories, their applications, and the processes involved in their production can help industries choose the right materials for their specific needs, ensuring optimal performance and longevity of their high-temperature equipment.
Comentários