Understanding the Density of Lightweight Castable Refractories
- keruirefra
- 2024年9月25日
- 讀畢需時 6 分鐘
Lightweight castable refractories have become essential materials in various high-temperature applications, particularly in the steel, cement, and petrochemical industries. They are designed to withstand extreme thermal conditions while offering the advantages of lower weight and thermal insulation. One of the critical properties that determine the performance and suitability of lightweight castables is their density. This article explores the concept of density in lightweight castable refractories, factors affecting their density, and the implications of density on performance and application.
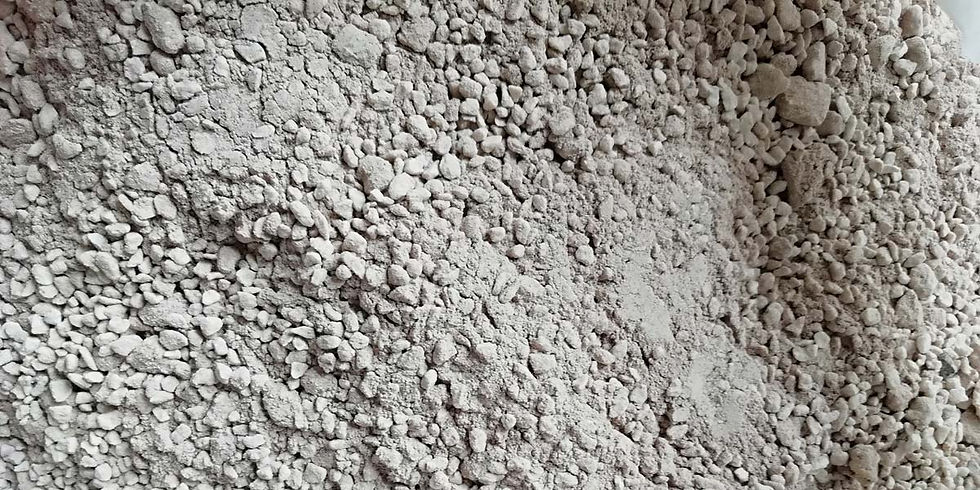
What is Lightweight Castable Refractory?
Lightweight castable refractories are a type of refractory material that can be poured into molds to form shapes that withstand high temperatures. Unlike traditional dense refractories, light weight castables are designed to have a lower density while maintaining structural integrity and thermal performance. This reduction in weight offers several benefits, including easier handling, reduced thermal mass, and improved thermal efficiency.
Composition of Lightweight Castables
The primary components of lightweight castables typically include:
Refractory Aggregates: Lightweight aggregates such as perlite, vermiculite, or expanded clay aggregate are commonly used. These aggregates significantly reduce the overall weight of the castable while maintaining thermal resistance.
Cement: The binder, usually a hydraulic or alumina cement, provides strength and helps the castable set and harden.
Additives: Various additives can be incorporated to enhance properties such as workability, strength, and resistance to thermal shock. These may include superplasticizers, fibers, and retarders.
Water: The amount of water added influences the workability and density of the castable mix.
The Concept of Density
Definition of Density
Density is defined as mass per unit volume. It is a fundamental property of materials that can significantly affect their performance in various applications. For lightweight castables, density is typically measured in kilograms per cubic meter (kg/m³) or pounds per cubic foot (lb/ft³).
Importance of Density in Lightweight Castables
The density of lightweight castable refractories is crucial for several reasons:
Thermal Performance: Density influences the thermal conductivity of the material. Lower density materials tend to have better insulating properties, which can improve energy efficiency in high-temperature applications.
Mechanical Strength: While lightweight castables are designed to be less dense, their density still plays a role in their compressive and flexural strength. A balance between lightweight properties and adequate strength must be achieved.
Handling and Installation: Lower density materials are easier to handle and install, reducing labor costs and improving overall efficiency in construction.
Cost-Effectiveness: Lightweight castables can lead to cost savings in transport and installation due to their reduced weight.

Measuring Density of Lightweight Castables
The density of lightweight castables can be determined using various methods, with the most common being the water displacement method or by using a density meter.
Water Displacement Method
Preparation: A sample of the castable is dried and weighed (mass A).
Displacement: The sample is submerged in a known volume of water, and the volume of displaced water is measured.
Calculation: The density can be calculated using the formula:
Density=Mass of the SampleVolume of Displaced Water\text{Density} = \frac{\text{Mass of the Sample}}{\text{Volume of Displaced Water}}Density=Volume of Displaced WaterMass of the Sample
This method provides an accurate measurement of density, accounting for any air pockets that may be present in the castable.
Using Density Meters
Advanced density meters utilize various technologies, such as gamma-ray or X-ray techniques, to measure the density of materials non-destructively. These methods can offer quick and reliable results, particularly in industrial settings.
Factors Affecting the Density of Lightweight Castables
Several factors influence the density of lightweight castable refractories:
1. Type of Aggregates
The choice of aggregates has a significant impact on the density of the castable. Lightweight aggregates, such as expanded perlite or pumice, reduce the overall density compared to traditional dense aggregates like bauxite or andalusite.
2. Binder Content
The type and amount of binder used also affect the density. Higher cement content can lead to increased density, while lower binder content can reduce density. Finding the right balance is essential for achieving desired performance characteristics.
3. Water-to-Binder Ratio
The water-to-binder ratio influences both the workability and density of the castable mix. A higher water content typically results in a lower density after curing, but excessive water can compromise the strength and integrity of the final product.
4. Mixing Process
The mixing process itself can influence the density of the castable. Adequate mixing ensures even distribution of aggregates and binders, preventing air entrapment, which can increase density inconsistencies.
5. Curing Conditions
Curing conditions, including temperature and humidity, can affect the density of the hardened castable. Proper curing is essential to achieving the intended density and strength.
Typical Density Ranges for Lightweight Castables
The density of lightweight castable refractories can vary widely, typically ranging from 800 kg/m³ to 1800 kg/m³ (50 lb/ft³ to 112 lb/ft³).
Low-Density Lightweight Castables: These have a density of around 800 kg/m³ to 1200 kg/m³ (50 lb/ft³ to 75 lb/ft³) and are used primarily for applications requiring high insulation.
Medium-Density Lightweight Castables: Ranging from 1200 kg/m³ to 1600 kg/m³ (75 lb/ft³ to 100 lb/ft³), these castables balance insulation and strength, making them suitable for a variety of industrial applications.
High-Density Lightweight Castables: With densities from 1600 kg/m³ to 1800 kg/m³ (100 lb/ft³ to 112 lb/ft³), these castables offer increased mechanical strength while still providing some degree of insulation.
Performance Implications of Density
Thermal Conductivity
Density plays a crucial role in thermal conductivity. Lightweight castables with lower density typically exhibit lower thermal conductivity, enhancing their thermal insulation properties. This is particularly beneficial in applications like furnace linings, where maintaining high temperatures is critical while minimizing heat loss.
Mechanical Strength
While lightweight castables offer advantages in terms of weight and thermal insulation, they must also maintain adequate mechanical strength to withstand operational stresses. The density of the castable directly influences its compressive strength and overall durability. Therefore, a careful balance must be achieved to ensure that the castable can withstand thermal cycling, mechanical loading, and exposure to aggressive environments.
Resistance to Thermal Shock
The ability to withstand rapid temperature changes—thermal shock resistance—is vital for many applications. Generally, lower density materials demonstrate better resistance to thermal shock due to their ability to accommodate expansion and contraction without cracking. However, the specific formulation and quality of the lightweight castable also play significant roles.
Applications of Lightweight Castables
Lightweight castable refractories are utilized in various applications, including:
1. Furnace Linings
In industrial furnaces, lightweight castables provide insulation while protecting the structural integrity of the furnace. Their lower density reduces thermal mass, allowing for faster heating and energy savings.
2. Kilns
In ceramic and cement kilns, lightweight castables are used to line the kiln walls, minimizing heat loss and improving efficiency. Their thermal properties help maintain the necessary temperatures for optimal firing.
3. Boilers
Lightweight castables are also employed in boiler applications, where their insulating properties enhance efficiency and reduce fuel consumption.
4. Incinerators
In waste incineration, lightweight castables provide thermal insulation while resisting corrosive gases and high temperatures, ensuring the longevity of the incinerator linings.
5. Petrochemical Applications
In the petrochemical industry, lightweight castables are used in reactors and other high-temperature environments where thermal insulation and chemical resistance are critical.
Advantages of Lightweight Castables
1. Energy Efficiency
The thermal insulation properties of lightweight castables contribute to reduced energy consumption in high-temperature applications. By minimizing heat loss, they help maintain optimal operational temperatures.
2. Reduced Weight
The lower weight of lightweight castables simplifies handling and installation, reducing labor costs and improving overall efficiency during construction and maintenance.
3. Versatility
Lightweight castables can be formulated for various applications, allowing for customization to meet specific performance requirements. This versatility makes them suitable for diverse industrial settings.
4. Cost-Effectiveness
While the initial investment in lightweight castables may be higher than traditional materials, their long-term benefits, including reduced energy consumption and maintenance costs, often lead to significant savings.
Challenges and Considerations
Despite their numerous advantages, lightweight castables also present challenges:
1. Moisture Sensitivity
Lightweight castables can be sensitive to moisture, which may affect their performance and integrity. Proper handling and storage are essential to mitigate moisture-related issues.
2. Initial Cost
The production of high-quality lightweight castables can be costlier than traditional refractories, which may deter some manufacturers from using them. However, the overall benefits often justify the investment.
3. Performance Variability
Achieving consistent performance in lightweight castables can be challenging due to variations in raw materials, mixing processes, and curing conditions. Quality control is essential to ensure that the final product meets specified standards.
Conclusion
The density of lightweight castable refractories is a critical parameter that influences their performance, including thermal conductivity, mechanical strength, and resistance to thermal shock. Understanding the factors that affect density and its implications is vital for optimizing the use of lightweight castables in high-temperature applications.
Comments