Silicon Carbide Bricks for Ceramic Inudstry
- keruirefra
- 2024年10月16日
- 讀畢需時 4 分鐘
Silicon carbide (SiC) bricks are a critical component in the ceramic industry, particularly known for their exceptional thermal properties, mechanical strength, and chemical resistance. These bricks are widely used in high-temperature applications, including kilns and furnaces, where they contribute to efficient energy use and improved product quality. This article explores the characteristics, manufacturing processes, applications, advantages, and challenges associated with silicon carbide bricks in the ceramic industry.

Properties of Silicon Carbide Bricks
Chemical Composition
Silicon carbide bricks are primarily composed of silicon carbide, which is formed by the reaction of silicon and carbon at high temperatures. The purity of the SiC used in these bricks significantly influences their performance. Typically, high-purity SiC (over 98%) is preferred for applications requiring superior thermal and mechanical properties.
Physical Properties
High Thermal Conductivity: Silicon carbide exhibits excellent thermal conductivity, which allows for efficient heat transfer within kilns and furnaces. This property helps maintain uniform temperatures, reducing energy consumption.
High Melting Point: With a melting point exceeding 2700°C (4892°F), silicon carbide bricks can withstand extreme temperatures without deforming or losing structural integrity.
Chemical Resistance: SiC bricks demonstrate remarkable resistance to chemical attack from acids, alkalis, and molten glass. This characteristic prolongs the lifespan of kiln linings and reduces maintenance costs.
Mechanical Strength: Silicon carbide bricks possess high compressive strength and durability, making them suitable for demanding applications where mechanical wear is a concern.
Thermal Shock Resistance: These bricks can withstand rapid temperature changes without cracking or spalling, which is essential in environments where thermal cycling occurs frequently.
Manufacturing Process
The production of silicon carbide bricks involves several key steps:
Raw Material Selection
High-purity silicon and carbon sources are carefully selected to ensure optimal performance characteristics in the final product. The quality of these raw materials directly impacts the overall properties of the bricks.
Mixing
The selected raw materials are mixed in precise proportions to achieve the desired chemical composition. This step may involve adding binders or other additives to enhance specific properties such as strength or corrosion resistance.
Molding
The mixed material is then pressed into molds using hydraulic or mechanical presses. This process ensures that the bricks have a consistent density and low porosity, which are critical for performance.
Sintering
After molding, the bricks undergo a sintering process at high temperatures (around 2000°C) to facilitate the formation of silicon carbide crystals. This step enhances the mechanical strength and thermal stability of the bricks.
Quality Control
Rigorous testing is conducted throughout the manufacturing process to ensure that the bricks meet industry standards for physical and chemical properties. Tests may include assessments of density, porosity, thermal conductivity, and mechanical strength.
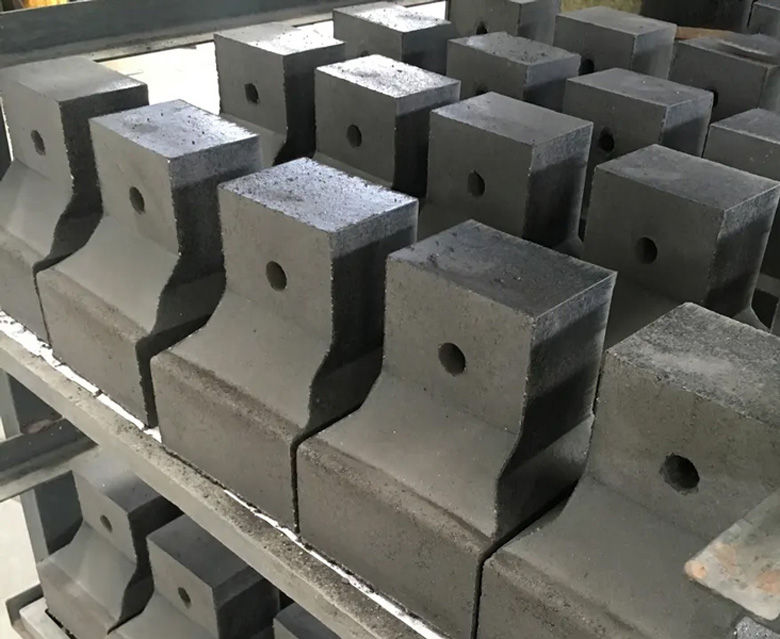
Applications in the Ceramic Industry
Silicon carbide bricks are extensively used across various applications in the ceramic industry:
1. Kiln Linings
Silicon carbide bricks are commonly employed as linings in ceramic kilns due to their high-temperature resistance and durability. They help maintain consistent temperatures during firing processes while minimizing heat loss.
2. Kiln Furniture
These bricks are also used to manufacture kiln furniture such as shelves and supports that hold ceramic products during firing. Their ability to withstand high temperatures without deforming makes them ideal for this application.
3. Glass Melting Furnaces
In glass production, silicon carbide bricks line melting furnaces where raw materials are transformed into molten glass. Their chemical resistance ensures that they can withstand corrosive environments without significant degradation.
4. Heat Exchangers
Silicon carbide's excellent thermal conductivity makes it suitable for use in heat exchangers within various industrial processes, including ceramics and glass manufacturing.
5. Sintering Furnaces
In sintering operations where powders are compacted and heated to form solid materials, SiC bricks provide reliable insulation and support due to their high strength and thermal stability.
Advantages of Silicon Carbide Bricks
Enhanced Durability: The exceptional mechanical properties of silicon carbide bricks lead to longer service life compared to traditional refractory materials, reducing replacement costs over time.
Energy Efficiency: High thermal conductivity minimizes energy consumption by improving heat transfer efficiency within kilns and furnaces.
Versatility: Silicon carbide bricks can be tailored for specific applications by adjusting their composition or manufacturing processes, making them suitable for various industrial uses.
Chemical Resistance: Their ability to resist chemical attack from aggressive materials ensures that they maintain structural integrity even in harsh environments.
Low Maintenance: The durability and resistance to wear reduce maintenance needs, allowing for more continuous operation in industrial settings.
Challenges Associated with Silicon Carbide Bricks
Despite their numerous advantages, silicon carbide bricks also face some challenges:
Cost Considerations: The initial cost of silicon carbide bricks can be higher than that of traditional refractory materials; however, this is often offset by their longer lifespan and reduced maintenance costs.
Brittleness: While SiC has high compressive strength, it can be brittle under certain conditions, which may lead to cracking if not handled properly during installation or operation.
Thermal Expansion Issues: Differences in thermal expansion rates between silicon carbide and other materials can lead to stress concentrations that may result in cracking over time if not managed appropriately.
Limited Availability: High-purity silicon carbide may not be readily available in all regions, potentially affecting supply chains for manufacturers reliant on these materials.
Recent Developments in Silicon Carbide Brick Technology
Innovations continue to enhance the performance of silicon carbide bricks:
Advanced Manufacturing Techniques: New methods such as additive manufacturing (3D printing) are being explored to create complex shapes that were previously difficult or impossible to achieve with traditional methods.
Improved Formulations: Research into alternative additives or composite materials aims to enhance specific properties such as thermal shock resistance or reduce brittleness without compromising other performance characteristics.
Sustainability Initiatives: Efforts are underway to develop more sustainable production processes that minimize environmental impact while maintaining high-quality standards for silicon carbide bricks.
Recycling Opportunities: Exploring recycling methods for used SiC materials can contribute to sustainability goals within the ceramic industry by reducing waste and promoting circular economy practices.
Conclusion
Silicon carbide bricks play an essential role in the ceramic industry due to their unique combination of high-temperature resistance, mechanical strength, chemical stability, and thermal conductivity. Their extensive applications range from kiln linings and furniture to glass melting furnaces and heat exchangers, making them indispensable in modern manufacturing processes.As technology advances and industries increasingly prioritize efficiency and sustainability, ongoing research into enhancing silicon carbide brick performance will likely yield further innovations that improve their utility across various applications within ceramics and beyond. Ultimately, these developments will contribute positively toward achieving higher quality products while minimizing environmental impact within the ceramic industry landscape.
Bình luận