What Are High Alumina Refractory Bricks?
- keruirefra
- 2月24日
- 讀畢需時 2 分鐘
High alumina refractory bricks are a type of advanced refractory material widely used in industries that require exceptional heat resistance, mechanical strength, and chemical stability. Composed primarily of alumina (Al₂O₃), these bricks are known for their ability to withstand extreme temperatures and harsh environments, making them a critical component in high-temperature industrial processes.

Composition and Manufacturing
High alumina bricks are made from raw materials with a high alumina content, typically ranging from 50% to 90% or higher. The manufacturing process involves:
Raw Material Selection: High-purity bauxite or alumina is chosen as the primary raw material.
Mixing and Forming: The raw materials are mixed with binders and shaped into bricks using pressing or extrusion techniques.
Firing: The high alumina refractory bricks are sintered at temperatures between 1400°C and 1600°C (2552°F and 2912°F) to achieve high density and strength.
Key Properties of High Alumina Bricks
High alumina bricks are valued for their unique combination of properties, which include:
High Refractoriness: They can withstand temperatures up to 1800°C (3272°F), making them suitable for extreme heat environments.
Excellent Mechanical Strength: They have high compressive strength, ensuring durability under heavy loads.
Superior Chemical Resistance: High alumina bricks are highly resistant to acids, alkalis, and molten metals, making them ideal for corrosive environments.
Thermal Shock Resistance: They can endure rapid temperature changes without cracking or spalling.
Abrasion Resistance: Their hardness and density make them resistant to wear and erosion.
Applications of High Alumina Bricks
Due to their outstanding properties, high alumina bricks are used in a wide range of industries, including:
1. Iron and Steel Industry
Blast Furnaces: Used in the lining of high-temperature zones.
Ladles and Tundishes: Ideal for containing and transporting molten metal.
Non-Ferrous Metal Processing: Used in furnaces for melting aluminum, copper, and other metals.
2. Glass Manufacturing
Glass Tank Furnaces: High alumina bricks line the melting zones, where they resist the corrosive effects of molten glass and alkali vapors.
Regenerators and Checkers: Their thermal stability improves the efficiency of heat recovery systems.
3. Petrochemical Industry
Reactor Linings: Protect reactors from corrosive chemicals and high temperatures.
Catalyst Supports: Used in chemical processes due to their inertness and durability.
4. Cement and Lime Industry
Rotary Kilns: Used in high-temperature zones to withstand thermal and chemical stresses.
5. Ceramics and Electronics
Kiln Furniture: Used to support ceramic products during firing.
Semiconductor Manufacturing: High alumina bricks are used in high-temperature processing equipment.
Advantages of High Alumina Bricks
Long Service Life: Their durability reduces the need for frequent replacements, lowering maintenance costs.
Energy Efficiency: Their low thermal conductivity helps conserve energy in high-temperature processes.
Versatility: Suitable for a wide range of applications across multiple industries.
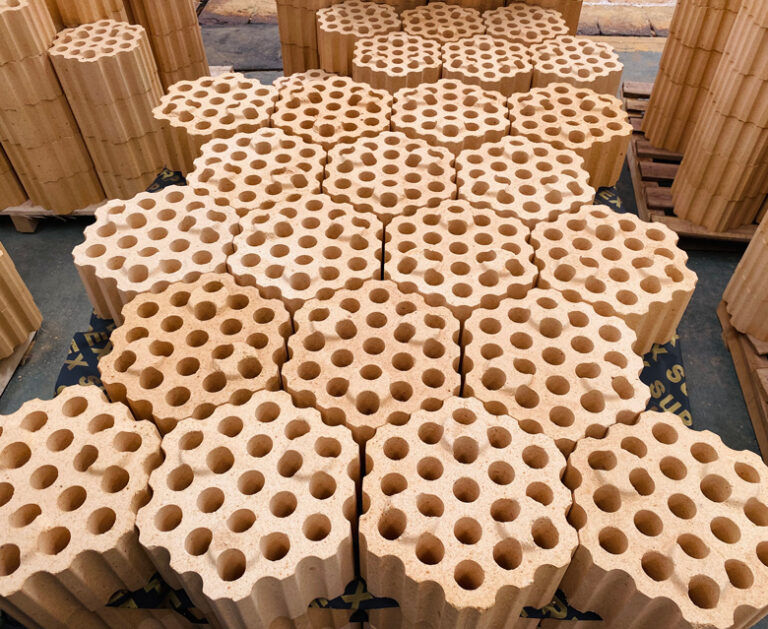
Conclusion
High alumina refractory bricks are a vital material in industries that demand extreme heat resistance, chemical stability, and mechanical strength. Their unique properties, including high refractoriness, thermal shock resistance, and abrasion resistance, make them indispensable in applications ranging from steelmaking and glass manufacturing to petrochemical processing and electronics. As industries continue to push the boundaries of temperature and performance, high alumina bricks will remain a key component in ensuring efficiency, durability, and safety.
Comments