Silica Fire Brick for Cement Furnace Applications
- keruirefra
- 2024年10月24日
- 讀畢需時 7 分鐘
Silica fire bricks, also known as silica refractory bricks, are among the most commonly used refractories in high-temperature applications, especially in furnaces and kilns. Their primary component is silicon dioxide (SiO₂), which gives them unique properties suitable for enduring the thermal and chemical conditions encountered in industrial furnaces, including cement furnaces.

Composition of Silica Fire Bricks
Silica fire bricks are composed predominantly of silicon dioxide, with SiO₂ content typically ranging from 93% to 97%. The primary raw material used in the production of these bricks is high-purity quartzite or sandstone. The chemical structure of SiO₂ allows silica fire bricks to have exceptional thermal stability, particularly at high temperatures.
In addition to silicon dioxide, silica fire bricks may also contain small amounts of alumina (Al₂O₃) and iron oxide (Fe₂O₃), which act as fluxing agents during the brick manufacturing process. These impurities, however, are typically minimized to ensure high refractoriness and to avoid compromising the brick's performance at elevated temperatures.
One of the distinctive features of silica bricks is their transformation behavior at high temperatures. Silica exists in various crystalline forms, including quartz, tridymite, and cristobalite, and these forms undergo phase transformations as the temperature increases. This characteristic allows silica bricks to perform well in cement furnaces where thermal cycling and extreme heat are regular occurrences.
Properties of Silica Fire Bricks
Silica fire bricks possess several properties that make them highly suitable for use in high-temperature industrial applications, such as cement furnaces. These properties include:
High Refractoriness: Silica fire bricks have a very high refractoriness, meaning they can withstand temperatures exceeding 1600°C. Their high melting point (about 1710°C) makes them particularly suitable for applications that involve prolonged exposure to extreme heat, such as in the burning zone of cement kilns.
Resistance to Thermal Expansion: One of the unique aspects of silica fire bricks is their low thermal expansion at high temperatures. Once the bricks are heated above 600°C, their coefficient of thermal expansion decreases, making them highly resistant to cracking and spalling when subjected to rapid temperature changes.
High Mechanical Strength: Silica fire bricks offer excellent mechanical strength at elevated temperatures. This property is crucial in cement furnaces, where the bricks must support heavy loads and resist the abrasive forces generated by the movement of raw materials and the rotation of the kiln.
Good Chemical Resistance: Silica fire bricks exhibit high resistance to acidic slags and fumes, which makes them ideal for furnaces where chemical corrosion from acidic compounds, such as sulfur, is a concern. However, they are less resistant to basic slags, and therefore, their use in environments where basic materials are prevalent is limited.
Thermal Conductivity: Silica fire bricks have moderate thermal conductivity, which helps them maintain the required thermal conditions inside the furnace without significant heat loss. This property is particularly important for ensuring energy efficiency and maintaining a stable temperature profile within the cement furnace.
Volume Stability at High Temperatures: Once silica fire bricks undergo the phase transformations mentioned earlier, they achieve excellent volume stability at high temperatures. This makes them resistant to deformation or shrinkage even after prolonged exposure to heat, a critical factor in maintaining the structural integrity of the cement furnace lining.
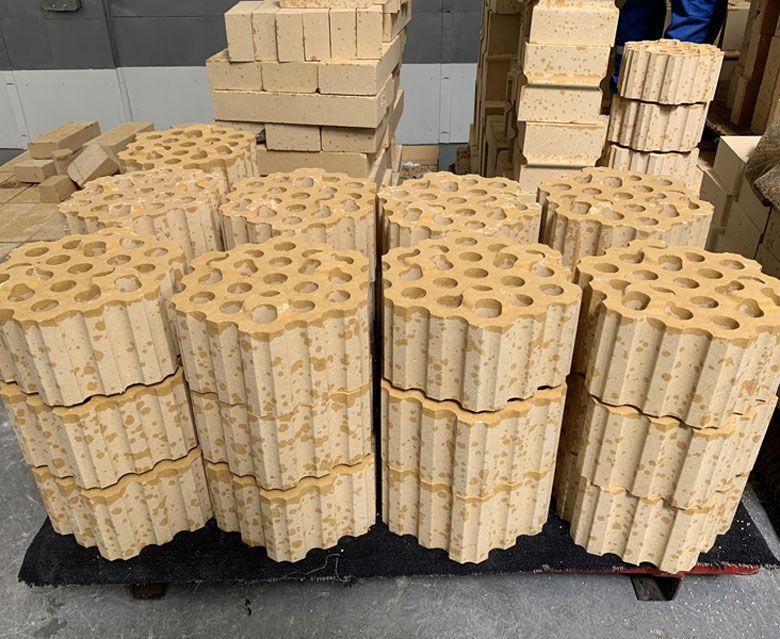
Manufacturing Process of Silica Fire Bricks
The production of silica fire bricks involves a series of carefully controlled steps to ensure that the final product meets the high standards required for use in cement furnaces. These steps include:
Raw Material Selection: High-purity quartzite or sandstone is chosen as the primary raw material. The purity of the silica content is critical for achieving high refractoriness and good mechanical properties in the final product.
Crushing and Grinding: The raw silica materials are crushed and ground into fine powder. This powder is then mixed with a binding agent, such as lime (CaO), which helps to bond the particles together during the firing process. In some cases, small amounts of alumina or iron oxide may be added to improve sintering.
Shaping: The silica mixture is shaped into bricks using hydraulic presses or extrusion methods. The pressing process compacts the material, ensuring that the brick has a dense structure with minimal porosity. The shape and size of the brick are tailored to the specific requirements of the cement furnace.
Drying: After shaping, the bricks are dried to remove any moisture present in the mixture. This step is crucial for preventing cracking or warping during the subsequent firing process.
Firing: The bricks are fired at high temperatures (usually between 1400°C and 1500°C) in a kiln. During the firing process, the silica undergoes phase transformations that give the brick its high refractoriness and thermal stability. The presence of lime acts as a flux, aiding in the sintering process and helping the silica particles bond together.
Cooling and Quality Control: Once the bricks have been fired, they are slowly cooled to prevent thermal shock. After cooling, the bricks undergo rigorous quality control tests to ensure they meet the required standards for refractoriness, mechanical strength, and chemical resistance. Only those bricks that pass these tests are deemed suitable for use in cement furnaces.
Applications of Silica Fire Bricks in Cement Furnaces
Cement furnaces, particularly rotary kilns, are one of the most demanding environments for refractory materials. These furnaces operate at extremely high temperatures and are subjected to various mechanical, chemical, and thermal stresses. Silica fire bricks are widely used in these furnaces due to their ability to withstand the harsh conditions encountered during the cement manufacturing process.
Lining of the Burning Zone: The burning zone of a rotary kiln is one of the hottest areas, where temperatures can reach up to 1500°C. Silica fire bricks are commonly used to line the burning zone because of their high refractoriness and resistance to thermal shock. Their ability to maintain structural integrity at high temperatures helps ensure the efficient operation of the furnace and prolongs the life of the refractory lining.
Lining of the Cooler Zone: After the burning zone, the clinker moves to the cooler zone, where it is rapidly cooled to a manageable temperature. Silica fire bricks are also used in this area due to their excellent resistance to thermal shock and ability to withstand the mechanical stress caused by the movement of the clinker. The bricks' low thermal expansion at high temperatures helps prevent cracking and ensures a long service life.
Preheater and Calciner: In modern cement plants, preheaters and calciners are used to preheat and partially calcine the raw materials before they enter the rotary kiln. Silica fire bricks are often used to line the preheater and calciner, where temperatures are slightly lower but still high enough to require refractory protection. The bricks' resistance to chemical attack from acidic gases, such as sulfur oxides, is particularly beneficial in these environments.
Transition Zones: The transition zones between different parts of the cement furnace, such as the area between the calciner and the rotary kiln, are also lined with silica fire bricks. These zones experience fluctuating temperatures and require refractory materials that can handle both thermal shock and mechanical stress. Silica fire bricks' ability to maintain their shape and strength under such conditions makes them an ideal choice for these areas.
Advantages of Using Silica Fire Bricks in Cement Furnaces
Silica fire bricks offer several advantages in cement furnace applications:
High Temperature Resistance: The ability of silica fire bricks to withstand temperatures exceeding 1600°C makes them ideal for use in the burning zone and other high-temperature areas of the cement furnace.
Cost-Effective: Silica fire bricks are relatively inexpensive compared to some other refractory materials, such as magnesia or alumina bricks. This makes them a cost-effective choice for lining large cement kilns, where large quantities of refractory bricks are required.
Durability: The low thermal expansion and high mechanical strength of silica fire bricks ensure a long service life, reducing the frequency of maintenance and replacement. This contributes to the overall efficiency and cost-effectiveness of cement kiln operations.
Good Resistance to Acidic Slags: In cement kilns, the presence of sulfur and other acidic compounds can cause chemical corrosion of the refractory lining. Silica fire bricks are highly resistant to acidic slags, helping to protect the kiln lining from chemical attack and prolonging its lifespan.
Stable Volume at High Temperatures: The phase transformations that occur in silica at high temperatures give silica fire bricks excellent volume stability. This means the bricks are less likely to shrink or deform during use, ensuring the structural integrity of the furnace lining.
Challenges of Using Silica Fire Bricks in Cement Furnaces
Despite their many advantages, there are also some challenges associated with using silica fire bricks in cement furnaces:
Sensitivity to Basic Slags: While silica fire bricks are resistant to acidic slags, they are less effective in environments where basic materials, such as lime, are present. In the cement industry, lime is a key component, and over time, the basic slags can erode the silica bricks, leading to wear and potential failure of the furnace lining.
Thermal Shock Sensitivity at Lower Temperatures: Although silica fire bricks have good thermal shock resistance at high temperatures, they are more vulnerable to thermal shock when exposed to rapid temperature changes at lower temperatures (below 600°C). This can be a concern during start-up and shut-down phases of the kiln operation.
Limited Application in Basic Environments: In cement kilns that process raw materials with a high lime content, basic refractories like magnesia or dolomite bricks may be preferred over silica fire bricks due to their superior resistance to basic slags. Therefore, the use of silica fire bricks may be limited to specific zones within the kiln where acidic conditions prevail.
Conclusion
Silica fire bricks are an essential refractory material in cement furnaces, particularly in the burning zone, cooler zone, and other high-temperature areas of the kiln. Their high refractoriness, mechanical strength, and resistance to thermal shock make them well-suited to the demanding conditions of cement manufacturing.
Comments