How to Choose the Right Magnesite Brick for Your Specific Industrial Needs
- keruirefra
- 3月12日
- 讀畢需時 4 分鐘
Magnesite bricks are a crucial component in various high-temperature industrial applications due to their exceptional refractory properties, including high heat resistance and chemical inertness. These bricks are widely used in industries such as steel, cement, glass, and non-ferrous metal production. However, selecting the right magnesite brick for specific industrial needs requires a thorough understanding of their properties, applications, and the factors influencing their performance. This article aims to provide a comprehensive guide on choosing the appropriate magnesite brick for different industrial applications.
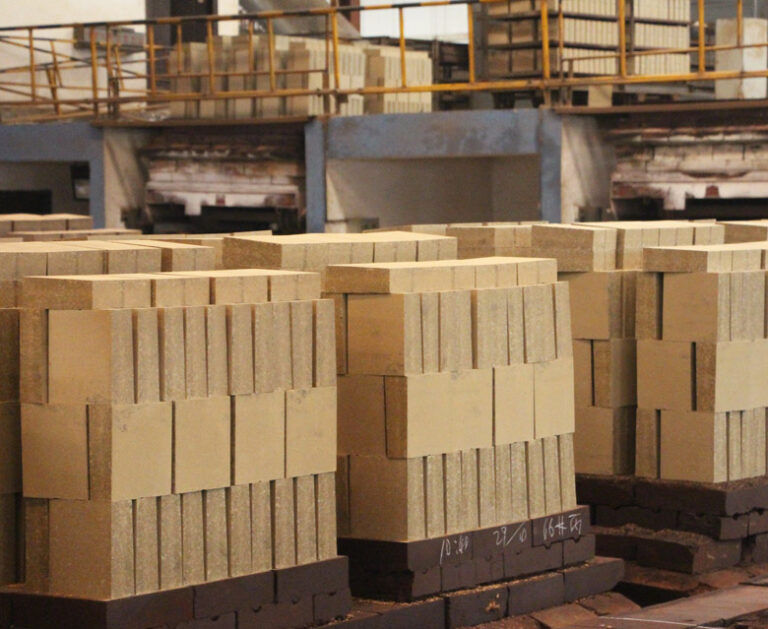
Introduction to Magnesite Bricks
Magnesite bricks are basic refractory materials composed primarily of magnesium oxide (MgO), with a content typically exceeding 90%. They are known for their high refractoriness, good alkali slag resistance, and ability to withstand extreme temperatures. The manufacturing process involves crushing, mixing, molding, and firing magnesia sand or clinker at high temperatures to produce sintered or fused magnesia bricks. Non-burnt magnesite bricks are made by adding chemical binders to magnesia and then drying the mixture.
Properties of Magnesite Bricks
High Refractoriness: Magnesite bricks can endure extremely high temperatures, often above 2000°C, making them ideal for applications in steelmaking furnaces and cement rotary kilns.
Alkali Resistance: They exhibit excellent resistance to alkali slag and chemical corrosion, which is crucial in environments where basic slags are present.
Thermal Stability: These bricks maintain their structural integrity under thermal shock conditions, ensuring reliability in operations with fluctuating temperatures.
Chemical Inertness: Magnesite bricks are chemically inert, which helps prevent contamination of the process materials in industries like glass production.
Applications of Magnesite Bricks
Magnesite bricks are versatile and find applications in several industries:
Steel Industry:
Basic Oxygen Furnaces (BOFs): Used as lining for the hearth and walls due to their resistance to basic slags and high temperatures.
Electric Arc Furnaces (EAFs): Employed as permanent lining for their durability and thermal stability.
Ladles: Magnesia bricks line ladles to protect against slag corrosion and maintain structural integrity.
Cement Industry:
Rotary Kilns: These bricks are used for lining rotary kilns in cement production due to their ability to withstand high temperatures and alkaline environments.
Glass Industry:
Glass Furnaces: Magnesite bricks are used in regenerators and as checker bricks for their heat resistance and minimal thermal expansion.
Non-Ferrous Metal Industry:
Smelting Furnaces: Employed in furnaces for copper, lead, zinc, and other non-ferrous metals due to their chemical inertness and high refractoriness.
Factors to Consider When Choosing Magnesite Bricks
Temperature Requirements: The operating temperature of the application dictates the type of magnesite brick needed. Higher purity bricks (e.g., M-98) are used for extremely high temperatures, while lower purity bricks (e.g., M-91) suffice for lower temperature applications.
Chemical Environment: The presence of basic slags or alkali requires bricks with high alkali resistance. Synthetic magnesite olivine bricks are particularly effective in such environments.
Mechanical Strength: Applications requiring high mechanical strength, such as ladle linings, necessitate bricks with higher cold crushing strength1.
Thermal Shock Resistance: In environments with frequent temperature fluctuations, bricks with superior thermal shock resistance are essential.
Cost and Availability: The cost of magnesite bricks varies based on purity and size. Balancing performance requirements with budget constraints is crucial.
Types of Magnesite Bricks
High-Purity Magnesia Bricks: These bricks have MgO content above 97% and are used in applications requiring extreme refractoriness and purity, such as in glass furnaces1.
Composite Magnesia Bricks: These bricks combine magnesia with other materials to enhance specific properties like thermal shock resistance or alkali resistance1.
Synthetic Magnesite Olivine Bricks: These bricks offer improved alkali resistance and environmental benefits, making them suitable for applications where sustainability is a priority.
Manufacturing Process and Quality Control
The manufacturing process of magnesite bricks involves several steps:
Raw Material Selection: High-quality magnesia sand or clinker is essential for producing bricks with desired properties.
Crushing and Mixing: The raw material is crushed and mixed with other additives if necessary.
Molding and Firing: The mixture is molded into the desired shape and fired at high temperatures to achieve the required refractoriness.
Quality control measures include testing for properties like bulk density, apparent porosity, and cold crushing strength to ensure the bricks meet industry standards.
Conclusion
Choosing the right magnesite brick for specific industrial needs involves understanding the properties and applications of these bricks. By considering factors such as operating temperature, chemical environment, mechanical strength, and cost, industries can optimize their processes and enhance efficiency. As technology advances and sustainability becomes more critical, innovative materials like synthetic magnesite olivine bricks are emerging as superior choices for high-temperature applications.
In summary, magnesite bricks are indispensable in various high-temperature industries due to their exceptional refractory properties. By selecting the appropriate type of magnesite brick based on specific application requirements, industries can ensure efficient and sustainable operations.
Future Developments and Trends
As industries continue to evolve, there is a growing demand for refractory materials that not only perform well under extreme conditions but also contribute to environmental sustainability. The development of new magnesite-based materials with enhanced properties and reduced environmental impact is expected to play a significant role in future industrial applications. Additionally, advancements in manufacturing technologies will likely improve the efficiency and cost-effectiveness of magnesite brick production.
Comments