Extruded Kiln Batts for Ceramic Kilns
- keruirefra
- 3月5日
- 讀畢需時 4 分鐘
Kiln batts, also known as kiln shelves or kiln furniture, are essential components in the ceramics, glass, and metallurgy industries. These flat, durable plates are used to support and separate ceramic or glass products during the firing process in kilns. Kiln batts must withstand extreme temperatures, thermal shock, and mechanical stress, making their material composition and design critical to their performance. This article provides a detailed overview of kiln batts, including their composition, manufacturing process, properties, and applications.
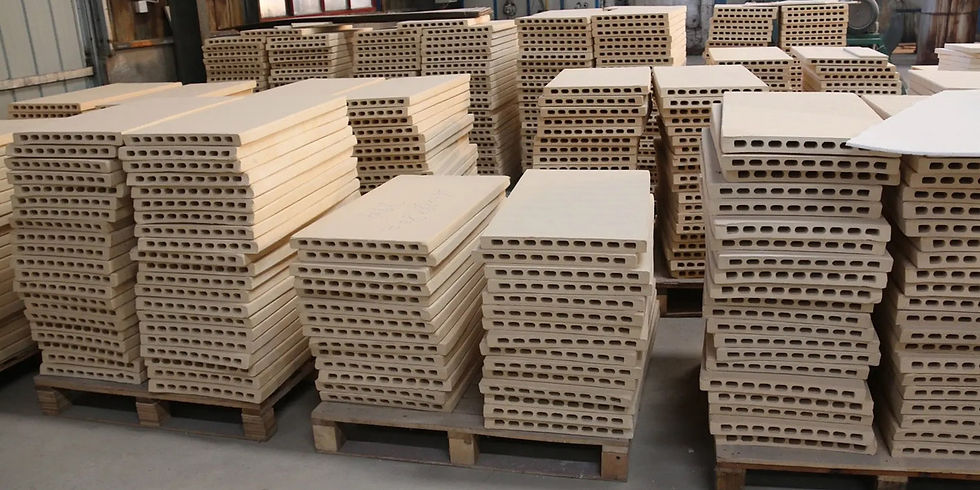
1. What Are Kiln Batts?
Kiln batts are flat, rigid plates made from refractory materials that are used to support ceramic or glass products during firing in kilns. They are designed to withstand high temperatures, thermal cycling, and mechanical loads while maintaining their structural integrity. Kiln batts are available in various shapes, sizes, and thicknesses to accommodate different types of kilns and products.
2. Composition and Structure
Kiln batts are made from high-quality refractory materials, including:
Cordierite: Known for its excellent thermal shock resistance and low thermal expansion.
Mullite: Provides high refractoriness and mechanical strength.
Silicon Carbide (SiC): Offers high thermal conductivity and resistance to wear and corrosion.
Alumina (Al₂O₃): Enhances mechanical strength and chemical stability.
The choice of material depends on the specific requirements of the application, such as maximum operating temperature, thermal shock resistance, and mechanical load.
3. Manufacturing Process
The production of kiln batts involves several key steps:
3.1 Raw Material Preparation
High-purity raw materials, such as cordierite, mullite, silicon carbide, or alumina, are selected and finely ground to ensure a homogeneous mixture. The raw materials are blended with binders and additives to achieve the desired composition.
3.2 Forming
The blended mixture is mixed with water and binders to form a plastic mass. This mass is then shaped into batts using pressing or extrusion techniques. The batts are formed to the required dimensions and thickness.
3.3 Drying
The formed batts are dried to remove moisture and prevent cracking during firing. This step is critical to ensure the batts' structural integrity.
3.4 Firing
The dried batts are fired in kilns at temperatures ranging from 1200°C to 1600°C (2192°F to 2912°F). During firing, the raw materials undergo a transformation, resulting in the formation of a dense, refractory microstructure.
3.5 Surface Treatment
The fired batts may undergo additional surface treatments, such as glazing or coating, to enhance their thermal and mechanical properties.
4. Key Properties of Kiln Batts
Kiln batts are valued for their unique combination of properties, which include:
4.1 High Refractoriness
Kiln batts can withstand temperatures up to 1600°C (2912°F), making them suitable for high-temperature firing processes.
4.2 Excellent Thermal Shock Resistance
The batts can endure rapid temperature changes without cracking or spalling, ensuring long-term durability in cyclic heating and cooling processes.
4.3 High Mechanical Strength
Kiln batts exhibit high compressive strength, ensuring durability under heavy loads and harsh conditions.
4.4 Low Thermal Expansion
The low thermal expansion of materials like cordierite minimizes the risk of warping or cracking during thermal cycling.
4.5 Chemical Stability
Kiln batts are highly resistant to acids, alkalis, and molten materials, making them ideal for corrosive environments.
4.6 Abrasion Resistance
Their hardness and density make them resistant to wear and erosion.
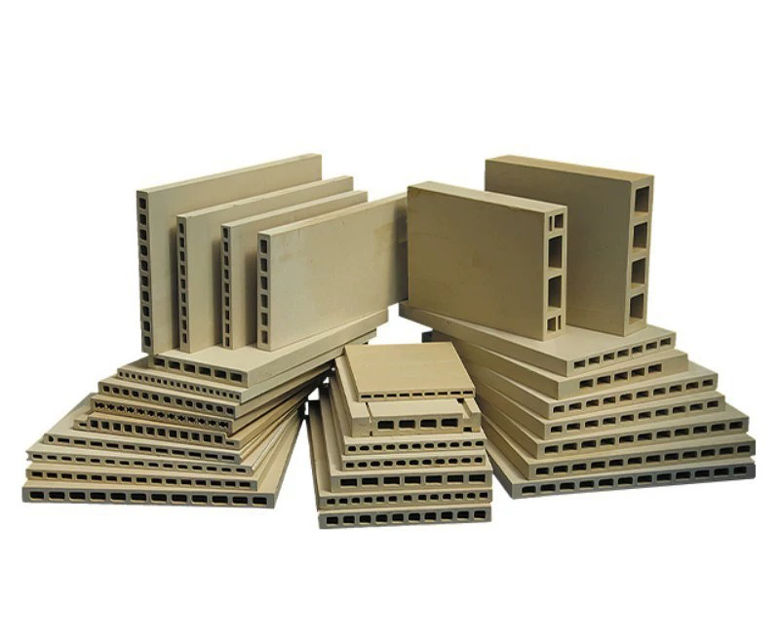
5. Applications of Kiln Batts
Kiln batts are widely used in various high-temperature industrial applications, including:
5.1 Ceramics Industry
Pottery and Tableware: Kiln batts are used to support pottery, tableware, and other ceramic products during firing.
Sanitaryware: They are used in the production of sanitaryware, such as toilets and sinks, to ensure even heating and prevent deformation.
Technical Ceramics: Kiln batts are used in the production of technical ceramics, such as insulators and substrates, where precise dimensional control is required.
5.2 Glass Industry
Glass Art: Kiln batts are used to support glass art pieces during firing, ensuring even heating and preventing sticking.
Glassware: They are used in the production of glassware, such as bottles and jars, to maintain consistent temperatures and prevent deformation.
5.3 Metallurgy Industry
Metal Casting: Kiln batts are used in the production of metal castings, where they support molds and cores during firing.
Heat Treatment: They are used in heat treatment processes to support metal parts during annealing, tempering, and hardening.
5.4 Electronics Industry
Semiconductor Manufacturing: Kiln batts are used in the production of semiconductors, where they support wafers and other components during high-temperature processing.
Electronic Components: They are used in the production of electronic components, such as capacitors and resistors, to ensure precise dimensional control.
5.5 Aerospace Industry
Composite Materials: Kiln batts are used in the production of composite materials, such as carbon fiber and ceramic matrix composites, where they support molds and preforms during curing and firing.
6. Advantages of Kiln Batts
Energy Efficiency: The low thermal conductivity of kiln batts helps conserve energy and reduce operational costs.
Long Service Life: Their durability reduces the need for frequent replacements, lowering maintenance costs.
Versatility: Suitable for a wide range of applications across multiple industries.
Improved Product Quality: Consistent temperatures and reduced thermal stress result in higher-quality products.
Reduced Downtime: The excellent thermal shock resistance of kiln batts minimizes the risk of cracking and spalling, reducing downtime and maintenance requirements.
7. Conclusion
Kiln batts are a vital material in industries that demand extreme heat resistance, chemical stability, and mechanical strength. Their unique properties, including high refractoriness, thermal shock resistance, and chemical stability, make them indispensable in applications ranging from ceramics and glass manufacturing to metallurgy and electronics. As industries continue to push the boundaries of temperature and performance, kiln batts will remain a key component in ensuring efficiency, durability, and safety.
Comments