Glass Reinforced Ceramic Cloth for Glass Furnaces
- keruirefra
- 2024年9月20日
- 讀畢需時 4 分鐘
Glass reinforced ceramic cloth has emerged as a revolutionary material in the glass manufacturing industry, particularly in the operation of glass furnaces. Its unique properties make it an ideal solution for high-temperature applications, providing durability, thermal insulation, and resistance to thermal shock. This article will explore the composition, manufacturing processes, applications, benefits, and future prospects of glass reinforced ceramic cloth in glass furnaces.
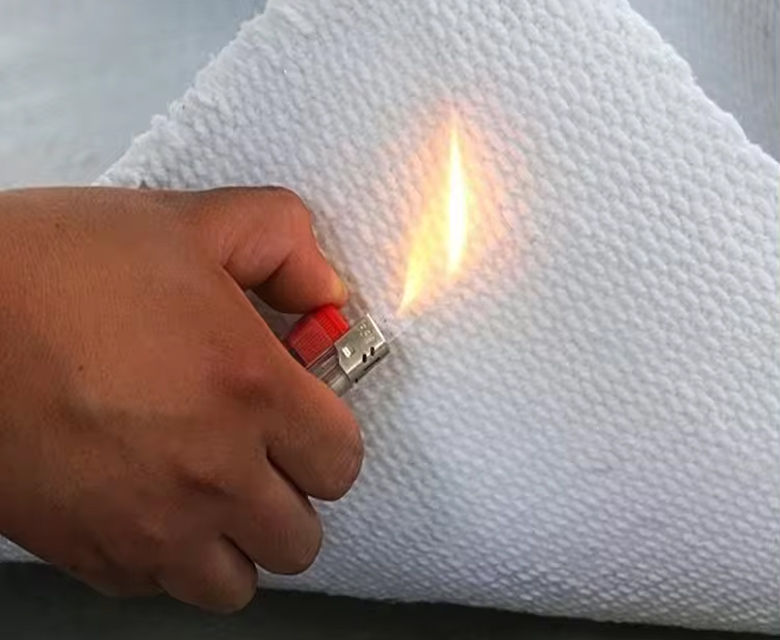
1. Understanding Glass Reinforced Ceramic Cloth
1.1 Composition
Glass reinforced ceramic cloth is composed of ceramic fibers that are woven into a cloth-like structure. The primary materials used in its production include:
Alumina Silicate Fibers: These fibers provide high-temperature resistance and excellent insulation properties.
Glass Fibers: Reinforcing fibers that enhance mechanical strength and thermal stability.
Binder Materials: Various types of binders may be used to ensure the fibers adhere together and maintain structural integrity.
1.2 Properties
The unique combination of materials results in several desirable properties:
High Thermal Resistance: Capable of withstanding temperatures up to 1,200°C (2,192°F) or higher without losing structural integrity.
Low Thermal Conductivity: Effective thermal insulator, which helps minimize heat loss in glass furnaces.
Flexibility and Workability: Can be easily cut and shaped to fit various applications within a furnace.
Chemical Resistance: Resistant to various chemicals encountered in glass manufacturing, including alkalis and acids.
2. Manufacturing Processes
2.1 Fiber Production
The first step in creating glass reinforced ceramic cloth is the production of the individual fibers. This typically involves the following processes:
Spinning: Alumina silicate and glass fibers are produced through a spinning process, where molten materials are extruded through fine orifices to form thin filaments.
Cooling and Solidification: The spun fibers are rapidly cooled and solidified to maintain their properties.
2.2 Weaving
Once the fibers are produced, they are woven together to form a cloth. This can be achieved through various weaving techniques, including:
Plain Weave: Simple over-under pattern providing basic strength and flexibility.
Satin Weave: Offers greater flexibility and a smoother surface, often used in applications requiring intricate shapes.
2.3 Finishing
After weaving, the cloth may undergo several finishing processes to enhance its properties:
Coating: Application of protective coatings to enhance chemical resistance or reduce friction.
Cutting and Shaping: The cloth can be cut into specific shapes or sizes required for particular applications in the glass furnace.
3. Applications in Glass Furnaces
3.1 Thermal Insulation
One of the primary applications of glass reinforced ceramic cloth in glass furnaces is thermal insulation. The material's low thermal conductivity helps to minimize heat loss, leading to improved energy efficiency. By insulating the furnace walls and other hot surfaces, manufacturers can reduce energy consumption and lower operating costs.
3.2 Furnace Linings
Glass reinforced ceramic cloth is used as a lining material in glass furnaces. Its high thermal resistance and flexibility allow it to conform to various shapes and surfaces within the furnace. This lining protects the structural components of the furnace from high temperatures and corrosive glass melts.
3.3 Expansion Joints
Glass reinforced ceramic cloth is ideal for use in expansion joints within glass furnaces. As temperatures fluctuate, materials expand and contract. The cloth can accommodate these movements without compromising the integrity of the furnace, preventing cracks and failures.
3.4 Seals and Gaskets
The flexibility and thermal stability of glass reinforced ceramic cloth make it suitable for seals and gaskets in high-temperature environments. These seals prevent the escape of heat and gases, contributing to the overall efficiency of the furnace.
3.5 Safety Blankets
In glass manufacturing, safety is paramount. Glass reinforced ceramic cloth can be used to create safety blankets that protect workers from heat exposure and accidental burns when working near hot surfaces.

4. Benefits of Glass Reinforced Ceramic Cloth
4.1 Energy Efficiency
The use of glass reinforced ceramic cloth in glass furnaces significantly improves energy efficiency. By minimizing heat loss, manufacturers can reduce fuel consumption, leading to lower operational costs and a reduced carbon footprint.
4.2 Enhanced Durability
Glass reinforced ceramic cloth exhibits excellent durability under extreme conditions. Its resistance to thermal shock and chemical corrosion ensures a longer lifespan compared to traditional insulating materials, resulting in lower maintenance and replacement costs.
4.3 Versatility
The flexibility of glass reinforced ceramic cloth allows it to be used in various applications within the glass furnace. Its ability to be cut and shaped makes it suitable for both complex and simple geometries, adapting to the specific needs of different furnace designs.
4.4 Improved Safety
The high-temperature resistance of glass reinforced ceramic cloth enhances workplace safety. By providing effective insulation and protection, it reduces the risk of burns and heat-related accidents in glass manufacturing facilities.
5. Challenges and Considerations
5.1 Cost
While glass reinforced ceramic cloth offers numerous benefits, the initial cost can be higher than traditional insulating materials. Manufacturers must weigh the long-term savings from energy efficiency and durability against the upfront investment.
5.2 Installation Expertise
Proper installation of glass reinforced ceramic cloth requires skilled labor and expertise. Inadequate installation may lead to reduced performance and increased maintenance needs. Training and knowledge sharing among workers are essential to ensure effective application.
5.3 Compatibility with Existing Systems
When integrating glass reinforced ceramic cloth into existing furnace designs, compatibility with current materials and systems must be considered. Manufacturers may need to adjust their processes or designs to accommodate this new material effectively.
6. Future Prospects
6.1 Innovations in Material Science
As the demand for more efficient and sustainable manufacturing processes grows, ongoing research in material science will likely lead to further innovations in glass reinforced ceramic cloth. This may include the development of new fiber compositions, enhanced thermal properties, and improved manufacturing techniques.
6.2 Expanded Applications
The versatility of glass reinforced ceramic cloth may lead to expanded applications beyond glass furnaces. Potential uses in other high-temperature industries, such as aerospace, automotive, and petrochemical, could drive further growth and development.
6.3 Sustainability Initiatives
With increasing emphasis on sustainability, manufacturers may explore eco-friendly production methods for glass reinforced ceramic cloth. This could involve using recycled materials or developing biobased alternatives, aligning with global efforts to reduce environmental impact.
7. Conclusion
Glass reinforced ceramic cloth represents a significant advancement in materials used for glass furnaces. Its unique properties, including high thermal resistance, flexibility, and durability, make it an ideal choice for insulation, linings, seals, and safety applications. The benefits of using this material extend beyond immediate performance, contributing to energy efficiency, safety, and long-term cost savings.
Comments