What are the Main Features and Uses of Magnesia Bricks?
- keruirefra
- 2024年9月27日
- 讀畢需時 4 分鐘
Magnesia bricks, also known as magnesium oxide bricks, are a type of refractory material that plays a crucial role in various industrial applications, particularly in high-temperature environments. This article will delve into the main features of magnesia bricks, their composition, manufacturing process, and a wide array of uses, particularly in the metallurgical and construction industries.

Composition and Manufacturing
Magnesia bricks are primarily composed of magnesium oxide (MgO), which can be derived from natural minerals such as magnesite or synthetic sources. The purity of the magnesium oxide used significantly affects the performance characteristics of the bricks. High-purity magnesia bricks, typically containing more than 90% MgO, are preferred for most industrial applications.
Raw Materials
Magnesite: Naturally occurring mineral primarily composed of magnesium carbonate (MgCO₃). When subjected to heat, it decomposes into magnesium oxide.
Synthetic Sources: These are produced through the calcination of magnesium hydroxide or magnesium carbonate, which results in high-purity MgO.
Manufacturing Process
The manufacturing process of magnesia brick involves several key steps:
Crushing and Grinding: Raw materials are crushed and ground to achieve the desired particle size.
Calcination: The ground material is heated in a kiln to convert magnesium carbonate into magnesium oxide. This step is crucial as it enhances the properties of the final product.
Mixing with Binders: The calcined MgO is mixed with binders and other additives to improve the physical properties of the bricks.
Molding: The mixture is then shaped into bricks using hydraulic presses.
Drying and Firing: The molded bricks are dried to remove moisture and then fired at high temperatures to enhance their mechanical strength and thermal resistance.
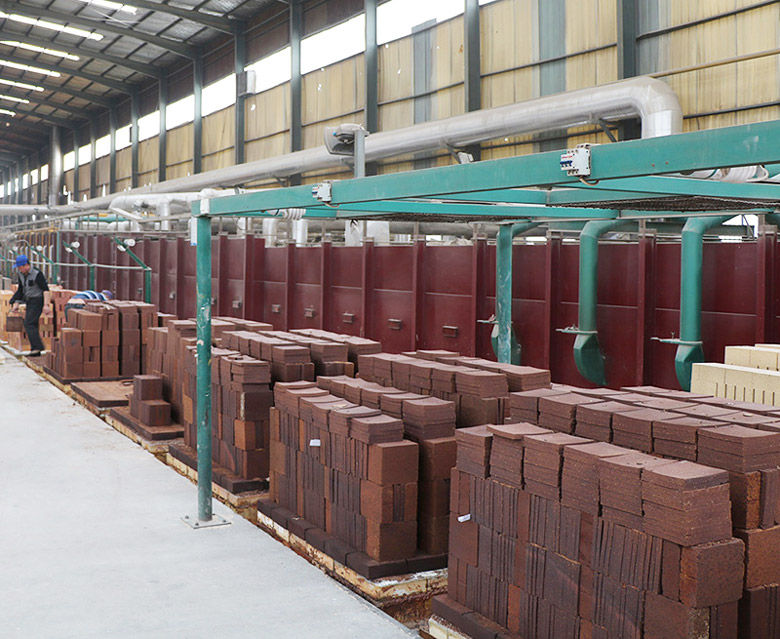
Main Features of Magnesia Bricks
Magnesia bricks possess a range of unique features that make them highly suitable for various industrial applications. Here are some of the most notable characteristics:
1. High Thermal Stability
Magnesia bricks can withstand extremely high temperatures, often exceeding 2000°C (3632°F). This makes them ideal for environments where thermal stability is paramount, such as in furnaces and kilns.
2. Excellent Refractoriness
These bricks exhibit excellent refractoriness, meaning they do not easily deform or melt under high temperatures. This property is essential for maintaining structural integrity in high-heat applications.
3. Resistance to Chemical Attack
Magnesia bricks are highly resistant to chemical corrosion, particularly against basic slags and fluxes. This feature is especially valuable in metallurgical processes where materials can be reactive.
4. Good Mechanical Strength
Despite being lightweight, magnesia bricks offer good mechanical strength, making them suitable for applications that require durability under stress.
5. Low Thermal Conductivity
The low thermal conductivity of magnesia bricks helps in minimizing heat loss, which is beneficial for energy efficiency in industrial processes.
6. Versatility
Magnesia bricks can be produced in various forms, including standard bricks, shaped bricks, and special-sized products, allowing for flexibility in different applications.
7. Eco-Friendly
When sourced from natural magnesite, magnesia bricks are considered more environmentally friendly compared to some other refractory materials, as they can be produced with a lower carbon footprint.
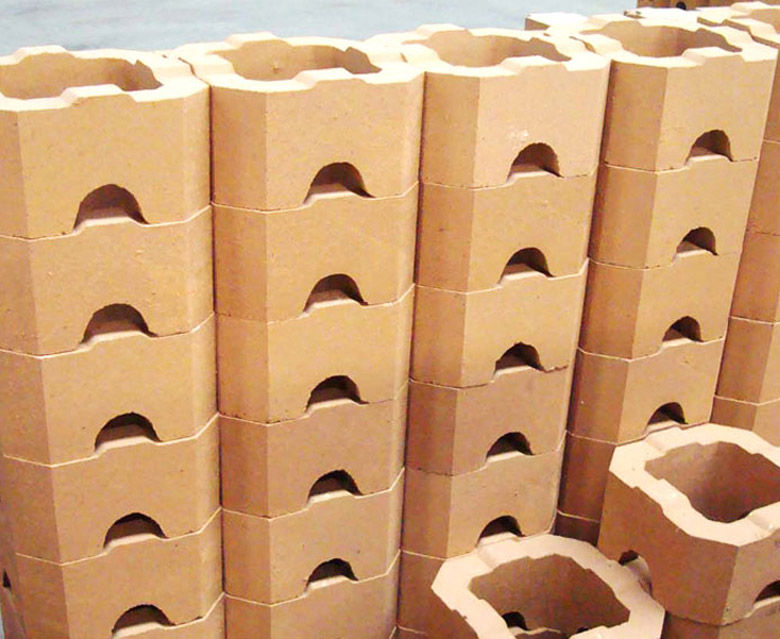
Uses of Magnesia Bricks
Magnesia bricks are used in a wide range of industries due to their unique properties. Below are some of the primary applications:
1. Metallurgical Industry
The metallurgical sector is the largest consumer of magnesia bricks. They are extensively used in:
Steelmaking: Magnesia bricks are employed in the lining of basic oxygen furnaces (BOFs) and electric arc furnaces (EAFs) due to their resistance to basic slags and high temperatures.
Non-Ferrous Metal Production: They are also utilized in the production of non-ferrous metals, such as copper and aluminum, where thermal and chemical resistance is critical.
2. Cement Industry
In the cement industry, magnesia bricks are used in rotary kilns where the temperature can reach up to 1500°C (2732°F). Their thermal stability and resistance to chemical attack make them ideal for the harsh conditions of cement production.
3. Glass Industry
The glass manufacturing process involves high temperatures and corrosive environments. Magnesia bricks are used to line glass melting furnaces, where they help maintain temperature and protect the furnace structure.
4. Chemical Processing
In chemical processing, magnesia bricks serve as linings for reactors and kilns. Their ability to withstand high temperatures and resist chemical attack makes them suitable for various chemical processes.
5. Power Generation
Magnesia bricks are also used in power generation, particularly in the lining of coal-fired boilers and gasification units. They help improve efficiency by maintaining high temperatures and reducing heat loss.
6. Incinerators
Magnesia bricks are employed in the construction of incinerators for waste management. Their thermal stability and resistance to corrosive gases make them ideal for enduring the extreme conditions found in waste incineration.
7. Industrial Ovens and Furnaces
Various industrial ovens and furnaces utilize magnesia bricks for insulation and lining, particularly in applications requiring high thermal efficiency.
Advantages of Using Magnesia Bricks
1. Cost-Effectiveness
While the initial investment for magnesia bricks may be higher than for some other materials, their durability and long lifespan can lead to significant cost savings over time, particularly in high-usage applications.
2. Energy Efficiency
The thermal properties of magnesia bricks contribute to energy savings in industrial processes. By minimizing heat loss, companies can reduce fuel consumption and operational costs.
3. Enhanced Performance
The unique features of magnesia bricks enable them to outperform other refractory materials in specific applications, particularly where high temperatures and chemical resistance are essential.
Challenges and Considerations
Despite their advantages, the use of magnesia bricks comes with certain challenges:
1. Sensitivity to Water
Magnesia bricks can be sensitive to water, which can lead to hydration and degradation. Proper storage and handling are crucial to maintain their integrity.
2. Limited Availability of High-Purity Magnesite
The availability of high-purity magnesite can sometimes be a limiting factor in the production of high-quality magnesia bricks. This scarcity can lead to fluctuations in pricing and supply.
3. Environmental Concerns
While magnesia bricks are generally considered eco-friendly, the mining and processing of raw materials can have environmental impacts that need to be managed responsibly.
Conclusion
Magnesia bricks are indispensable in various high-temperature industrial applications, thanks to their exceptional properties such as high thermal stability, chemical resistance, and mechanical strength. From the metallurgical sector to power generation and glass manufacturing, their versatility makes them a preferred choice for many industries.
Comments