What Are Mullite Refractory Bricks Made Of
- keruirefra
- 2024年8月29日
- 讀畢需時 3 分鐘
Mullite refractory bricks are a type of high-alumina refractory material with mullite (3Al2O3·2SiO2) as the main crystal phase. These bricks typically contain between 65% and 80% alumina content. Mullite bricks are known for their excellent refractory properties, making them suitable for use in various high-temperature applications such as glass furnaces, hot blast stoves, and ceramic furnaces. Know what are mullite refractory bricks made of.
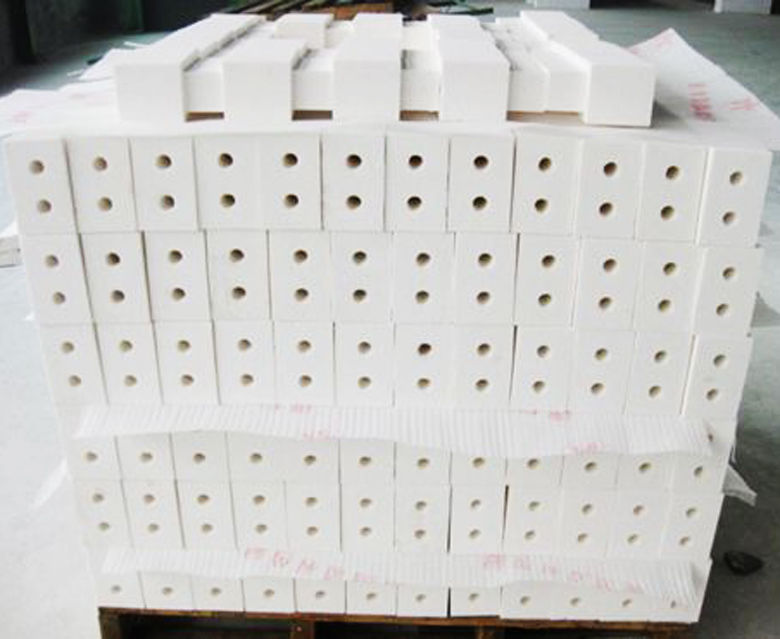
Raw Materials for Mullite Refractory Bricks
The primary raw materials used in the production of mullite refractory bricks are:
Bauxite: A mineral composed primarily of aluminum oxide (Al2O3), bauxite is the main source of alumina in mullite bricks.
Silica (SiO2): Silica, typically in the form of sand or quartz, provides the silicon oxide component necessary for the formation of mullite.
Alumina (Al2O3): In addition to bauxite, pure alumina may be added to increase the overall alumina content of the brick.
Fireclay: Fireclay is a refractory clay that acts as a binder and helps in the formation of mullite during firing.
Additives: Depending on the specific requirements, various additives such as zirconia (ZrO2) may be incorporated to enhance certain properties like thermal shock resistance.
Manufacturing Process of Mullite Refractory Bricks
The manufacturing process of mullite refractory bricks typically involves the following steps:
Raw material preparation: The raw materials are crushed, ground, and sieved to obtain the desired particle size distribution.
Mixing and batching: The prepared raw materials are weighed and mixed thoroughly to ensure a homogeneous blend.
Forming: The mixed batch is then formed into the desired shape using various methods such as pressing, extrusion, or casting.
Drying: The formed bricks are dried to remove any residual moisture and prevent cracking during firing.
Firing: The dried bricks are fired at high temperatures, typically between 1500°C and 1800°C, to promote the formation of mullite and achieve the desired properties.
There are two main types of mullite refractory bricks based on the manufacturing process:
Sintered mullite bricks: These bricks are made by pressing and firing a mixture of bauxite, fireclay, and other raw materials.
Fused cast mullite bricks: Fused cast mullite bricks are produced by melting a mixture of high-alumina raw materials, such as bauxite and alumina, in an electric furnace. The molten material is then cast into molds and allowed to solidify.
Properties of Mullite Refractory Bricks
Mullite refractory bricks possess several desirable properties that make them suitable for high-temperature applications:
High refractoriness: Mullite bricks have a refractoriness of up to 1790°C, making them suitable for use in high-temperature environments.
Good thermal shock resistance: Mullite bricks exhibit excellent resistance to thermal shock, allowing them to withstand rapid temperature changes without cracking or spalling.
High strength at elevated temperatures: Mullite bricks maintain their strength and integrity even at high temperatures, ensuring the structural integrity of the refractory lining.
Resistance to corrosion and erosion: Mullite bricks are resistant to corrosion by various slags and glass liquids, as well as wear and erosion at high temperatures.
Low thermal expansion coefficient: The low thermal expansion coefficient of mullite bricks helps minimize the risk of cracking and spalling during thermal cycling.

Applications of Mullite Refractory Bricks
Mullite refractory bricks find extensive use in various high-temperature industries due to their excellent refractory properties. Some of the common applications include:
Glass industry: Mullite bricks are used in the construction of glass furnaces, particularly in the regenerative chamber, where they are exposed to high temperatures and corrosive glass melts.
Iron and steel industry: Mullite bricks are used in the construction of hot blast stoves and blast furnaces, where they are subjected to high temperatures and thermal cycling.
Ceramic industry: Mullite bricks are used in the lining of ceramic high-temperature furnaces, such as those used for the production of advanced ceramics and refractories.
Cement industry: Mullite bricks are used in the construction of cement kilns, where they are exposed to high temperatures and corrosive environments.
Conclusion
Mullite refractory bricks are a crucial component in various high-temperature industries due to their excellent refractory properties. These bricks are primarily made from bauxite, silica, alumina, and fireclay, with the specific composition varying depending on the desired properties and application. Mullite bricks are manufactured using either the sintering or fused casting process, resulting in a material with high refractoriness, good thermal shock resistance, and resistance to corrosion and erosion. The unique properties of mullite bricks make them indispensable in industries such as glass, iron and steel, ceramics, and cement, where they play a vital role in ensuring the efficiency and safety of high-temperature processes.
コメント