Refractory Checker Bricks for Blast Stoves: Enhancing Efficiency and Durability
- keruirefra
- 2024年6月27日
- 讀畢需時 4 分鐘
Refractory checker bricks play a pivotal role in the efficient operation of blast stoves, crucial components in industries such as steel manufacturing. These specialized bricks are meticulously designed to withstand extreme temperatures, thermal cycling, and chemical corrosion, ensuring the integrity and longevity of blast furnace linings. In this article, we delve into the significance of checker brick, their composition, manufacturing process, and their essential role in optimizing blast stove performance.
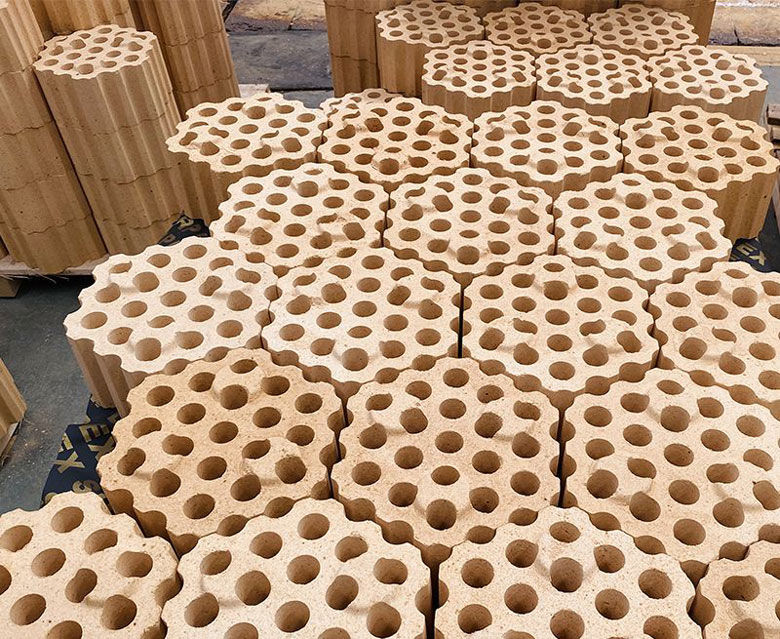
Introduction to Blast Stoves
Blast stoves, also known as blast furnaces, are colossal structures used primarily in the production of iron and steel. These furnaces operate at exceedingly high temperatures, often exceeding 1,500°C (2,732°F), where iron ore, coke, and limestone are smelted to produce molten iron and slag. The intense heat generated within blast stoves necessitates the use of robust refractory materials to line their interiors, providing thermal insulation, structural support, and protection against chemical erosion.
Role of Refractory Checker Bricks
Refractory checker bricks are specifically designed to enhance the efficiency and longevity of blast stoves. Positioned strategically within the lining, these bricks serve several critical functions:
Thermal Stability
The primary function of checker bricks is to provide thermal stability to the blast furnace lining. Their high refractoriness ensures that they can withstand the extreme temperatures generated during the smelting process without deforming or deteriorating. This property is crucial in maintaining the structural integrity of the furnace and preventing heat loss.
Thermal Cycling Resistance
Blast stoves undergo frequent heating and cooling cycles as they operate. Refractory checker bricks are engineered to withstand these thermal shocks, which can cause expansion and contraction of materials. Their composition and manufacturing process are optimized to minimize thermal stress and ensure consistent performance over prolonged periods.
Erosion and Corrosion Resistance
Chemical reactions within the blast furnace produce aggressive substances such as molten slag, which can erode refractory materials over time. Checker bricks are formulated with high alumina or silica content, enhancing their resistance to chemical corrosion and erosion. This durability ensures extended service life and reduces maintenance downtime, critical in continuous steel production operations.
Composition of Refractory Checker Bricks
The composition of refractory checker bricks varies depending on the specific requirements of the blast stove and the operating conditions. However, common components include:
High Alumina or Silica: Provides high refractoriness and resistance to thermal shock and chemical attack.
Clay or Bonding Agents: Enhances plasticity and cohesion during molding and drying processes.
Additives: Such as antioxidants or fluxes, tailored to improve performance under specific furnace conditions.
The precise combination and proportions of these materials are carefully selected to achieve the desired properties of strength, thermal stability, and resistance to corrosion.

Manufacturing Process
The manufacturing of refractory checker bricks involves several stages to ensure quality and consistency:
Raw Material Preparation: High purity raw materials such as alumina, silica, clay, and additives are carefully selected and blended to achieve the desired composition.
Forming: The blended materials are mixed with water to form a plastic mass, which is then molded into brick shapes using hydraulic presses or extrusion machines. This process ensures uniformity and density in the final product.
Drying: The molded bricks are dried in controlled atmospheres to remove excess moisture gradually. This step is crucial to prevent cracking or warping during subsequent firing.
Firing: The dried bricks undergo high-temperature firing in kilns or furnaces, typically exceeding 1,200°C (2,192°F). This firing process sinters the raw materials, causing them to bond and form the crystalline structure necessary for high strength and thermal stability.
Quality Control: Throughout each stage of manufacturing, rigorous quality control measures are implemented to verify dimensions, density, chemical composition, and physical properties of the checker bricks. This ensures compliance with industry standards and specifications.
Applications in Blast Stoves
Refractory checker bricks find extensive application in various zones of blast stoves:
Checkerwork: In the checkerwork pattern, where checker bricks are stacked alternately to create a lattice structure, they promote efficient heat exchange between incoming hot air and outgoing gases. This arrangement optimizes fuel combustion and reduces energy consumption.
Hot Blast Main: Positioned in the hot blast main, checker bricks regulate the flow and temperature of hot air entering the blast furnace. Their thermal stability and resistance to erosion ensure consistent and reliable operation of the furnace.
Stack Lining: Used in the lining of the blast stove stack, checker bricks provide structural support and thermal insulation. Their erosion resistance prolongs the lifespan of the stack lining, minimizing maintenance costs and downtime.
Advancements and Innovations
Continual research and development in refractory materials have led to innovations in checker brick design:
Nanostructured Materials: Incorporating nanotechnology to enhance the mechanical strength and thermal properties of checker bricks.
Advanced Bonding Agents: Utilizing advanced bonding agents to improve adhesion and reduce porosity, enhancing resistance to chemical attack.
Refractory Coatings: Applying specialized coatings to checker bricks to further enhance resistance to slag penetration and erosion.
Conclusion
Refractory checker bricks are indispensable components in the operation of blast stoves, ensuring efficient energy utilization, prolonged equipment lifespan, and consistent production in steel manufacturing and other industries. Their unique properties of thermal stability, thermal cycling resistance, and erosion resistance make them essential for maintaining the integrity and performance of blast furnace linings. As industries evolve and demand for high-performance refractories grows, ongoing advancements in materials science continue to drive innovations in checker brick design, further optimizing furnace efficiency and sustainability.
In conclusion, refractory checker bricks represent a critical link in the chain of technologies supporting modern steel production, offering reliability, durability, and performance in the most demanding industrial environments.
Commentaires