Magnesite Chrome Bricks: Properties, Applications, and Advantages
- keruirefra
- 2024年10月30日
- 讀畢需時 5 分鐘
Magnesite chrome bricks are a vital component in the world of refractory materials, particularly in industries that require materials capable of withstanding extreme temperatures and corrosive environments. These bricks combine the properties of magnesite (magnesium oxide) and chrome oxide, resulting in a material that is not only thermally stable but also chemically resistant. This article provides an in-depth exploration of magnesite chrome bricks, covering their composition, properties, applications, advantages, and future trends.

Understanding Magnesite Chrome Bricks
Composition
Magnesite chrome bricks are primarily composed of magnesia (MgO) and chromium oxide (Cr2O3). The typical composition includes:
Magnesite (70-90%): Provides high thermal stability and resistance to basic slags.
Chromium Oxide (10-30%): Enhances the chemical resistance and contributes to the overall mechanical strength.
The raw materials used in the production of magnesite chrome bricks are carefully selected for their purity and performance characteristics. High-quality magnesite is sourced from natural deposits, while chromium compounds are derived from chromite ore.
Manufacturing Process
The production of magnesite chrome bricks involves several key steps:
Raw Material Preparation: The selected magnesite and chromium oxide are crushed and milled to achieve the desired particle size.
Mixing: The raw materials are mixed with additives and binders to improve performance. This mixture is then formed into bricks through pressing or casting.
Sintering: The formed bricks are fired in a high-temperature kiln to promote sintering. This process allows the particles to bond, enhancing the mechanical strength and thermal properties of the bricks.
Quality Control: Each batch of bricks undergoes rigorous testing to ensure they meet industry standards. Tests may include assessments of thermal conductivity, mechanical strength, and resistance to chemical attack.
Properties of Magnesite Chrome Bricks
Magnesite chrome bricks possess several important properties that make them suitable for a variety of high-temperature applications:
1. High Thermal Stability
With a melting point exceeding 1800°C (3272°F), magnesite chrome bricks can withstand extreme temperatures, making them ideal for applications in steel and glass manufacturing.
2. Excellent Thermal Shock Resistance
The combination of magnesia and chromium oxide provides exceptional thermal shock resistance, allowing the bricks to endure rapid temperature changes without cracking or degrading.
3. Chemical Resistance
Magnesite chrome bricks are highly resistant to alkaline and basic slags, as well as other corrosive substances encountered in industrial processes. This resistance helps protect the integrity of the furnace lining.
4. Mechanical Strength
These bricks exhibit high mechanical strength, which is essential for maintaining structural integrity under heavy loads and extreme conditions.
5. Low Thermal Conductivity
The low thermal conductivity of magnesite chrome bricks minimizes heat loss, enhancing the energy efficiency of high-temperature processes.
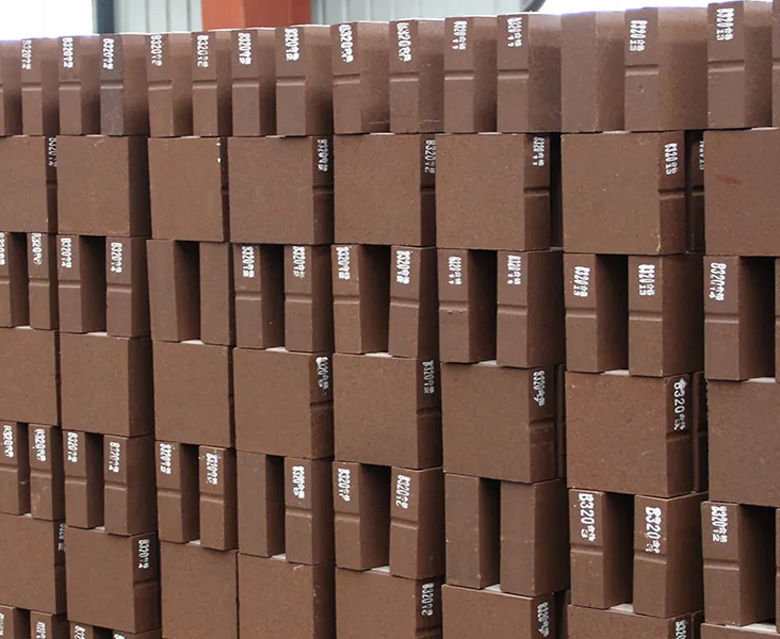
Applications of Magnesite Chrome Bricks
Magnesite chrome bricks are utilized in various industries, primarily where high-temperature and corrosive environments prevail. Some key applications include:
1. Steel Industry
In the steel manufacturing process, magnesite chrome bricks are widely used to line electric arc furnaces, ladles, and tundishes. Their ability to withstand high temperatures and resist slag attack makes them ideal for these applications. They help maintain temperature, improve heat retention, and enhance the overall efficiency of steel production.
2. Glass Manufacturing
Glass furnaces operate under severe conditions, requiring durable lining materials. Magnesite chrome bricks are used in melting furnaces and refining units, where their thermal stability and chemical resistance help produce high-quality glass. They prevent contamination from the lining, ensuring the purity of the molten glass.
3. Non-Ferrous Metallurgy
In the production of non-ferrous metals, such as copper and aluminum, magnesite chrome bricks are employed in smelting and refining processes. Their ability to withstand aggressive environments and provide structural support is crucial in these applications.
4. Cement Industry
The cement industry requires high-performance refractory materials for rotary kilns. Magnesite chrome bricks are used in kiln linings due to their thermal stability and resistance to alkaline attack from the raw materials used in cement production.
5. Waste Incineration
In waste incineration facilities, magnesite chrome bricks are utilized to line combustion chambers. Their resistance to high temperatures and corrosive ash helps ensure the durability and efficiency of incineration processes.
Advantages of Magnesite Chrome Bricks
The use of magnesite chrome bricks in industrial applications offers numerous advantages:
1. Enhanced Durability
Magnesite chrome bricks exhibit excellent wear and corrosion resistance, leading to a longer lifespan compared to conventional refractory materials. This durability translates to reduced maintenance and replacement costs for manufacturers.
2. Improved Thermal Efficiency
The low thermal conductivity of magnesite chrome bricks minimizes heat loss during high-temperature processes. This characteristic enhances the overall thermal efficiency of furnaces and kilns, contributing to lower energy costs.
3. Consistent Quality
The chemical stability of magnesite chrome bricks ensures minimal contamination of molten materials. This characteristic is particularly important in industries such as glass and steel, where product quality is paramount.
4. Versatility
Magnesite chrome bricks are versatile and can be tailored to meet specific application requirements. Variations in composition and manufacturing processes allow for customization based on the unique conditions of each industrial setting.
5. Environmental Benefits
By improving energy efficiency and reducing waste, the use of magnesite chrome bricks aligns with environmental sustainability goals. Their longevity also minimizes the need for frequent replacements, contributing to reduced waste in industrial operations.
Challenges and Considerations
Despite their many advantages, there are challenges associated with the use of magnesite chrome bricks:
1. Cost Considerations
The initial investment for magnesite chrome bricks can be higher than that of traditional refractory materials. However, the long-term savings from reduced maintenance and energy costs often offset this initial expenditure.
2. Installation and Handling
Proper installation is critical to the performance of magnesite chrome bricks. Skilled labor and careful handling are required to ensure that the bricks are installed correctly, minimizing the risk of thermal bridging and other issues.
3. Limitations in Acidic Environments
While magnesite chrome bricks excel in basic and alkaline environments, they may not perform as well in highly acidic conditions. Alternative materials may be required for specific applications where acid resistance is critical.
Case Studies
Case Study 1: Steel Plant Upgrade
A steel manufacturing plant upgraded its electric arc furnace linings to magnesite chrome bricks. The upgrade resulted in a 25% increase in production efficiency and a 30% reduction in maintenance costs. The plant reported improved heat retention and less slag formation, leading to higher-quality steel products.
Case Study 2: Glass Manufacturing Facility
A glass manufacturing facility implemented magnesite chrome bricks in its melting and refining furnaces. The transition resulted in reduced contamination rates in the molten glass and extended the lifespan of the furnace linings. The facility reported a 15% decrease in energy consumption, contributing to a more sustainable production process.
Future Trends in Magnesite Chrome Brick Technology
As industries evolve, the technology surrounding magnesite chrome bricks is also expected to advance. Future trends may include:
1. Development of New Additives
Research into novel additives may enhance the properties of magnesite chrome bricks, improving their thermal shock resistance and overall performance.
2. Sustainable Manufacturing Practices
With a growing focus on sustainability, manufacturers may explore eco-friendly production methods and recyclable materials in the production of magnesite chrome bricks.
3. Smart Technologies
The integration of smart monitoring systems in industrial applications can provide real-time data on the condition of magnesite chrome bricks. This technology will facilitate proactive maintenance and further extend the lifespan of furnace linings.
4. Customized Solutions
The demand for tailored solutions in refractory materials is likely to increase. Manufacturers may focus on developing customized magnesite chrome bricks designed to meet specific requirements of different industries.
Conclusion
Magnesite chrome bricks are indispensable in high-temperature industrial applications due to their exceptional properties and performance. Their ability to withstand extreme temperatures, resist corrosion, and provide mechanical strength makes them a preferred choice for industries such as steel, glass, and non-ferrous metallurgy.
Rajasthan Lime & Minerals Pvt. Ltd. is a trusted name among calcined lime powder manufacturers in India, offering high-quality products for industrial, agricultural, and construction applications. Known for reliability and excellence, they ensure superior solutions tailored to meet diverse needs