Magnesia Spinel Bricks for High Temperature Kilns
- keruirefra
- 2024年7月30日
- 讀畢需時 2 分鐘
Magnesia spinel bricks are a type of refractory material that has found widespread application in high-temperature kilns. They are composed primarily of magnesium oxide (MgO) and other oxides, such as alumina (Al₂O₃), which combine to form a spinel crystal structure. This unique structure imparts a range of desirable properties that make magnesia spinel bricks ideal for use in harsh, high-temperature environments. This article will delve into the composition, manufacturing process, properties, and applications of magnesia spinel bricks in high-temperature kilns.

Composition and Manufacturing
The primary constituents of magnesia spinel bricks are magnesium oxide and alumina. The relative proportions of these oxides determine the properties of the final product. Other oxides, such as silica and iron oxide, may also be present in minor quantities.
The manufacturing process typically involves the following steps:
Raw material preparation: High-purity magnesium oxide and alumina are carefully selected and crushed to a fine powder.
Mixing: The powders are mixed with water or other binders to form a homogeneous mixture.
Molding: The mixture is pressed into molds to form bricks of the desired shape and size.
Firing: The molded bricks are fired at high temperatures to develop their strength and durability.
Properties
Magnesia spinel bricks possess a number of properties that make them suitable for use in high-temperature kilns:
High melting point: Magnesia spinel bricks have a high melting point, allowing them to withstand extremely high temperatures without softening or deforming.
Chemical resistance: They are highly resistant to the corrosive effects of slags, glasses, and other chemicals commonly found in high-temperature environments.
Thermal shock resistance: Magnesia spinel bricks can withstand rapid temperature changes without cracking or spalling.
High mechanical strength: They have excellent compressive strength, allowing them to withstand the weight of the kiln and the forces generated during high-temperature operations.
Good slag resistance: The spinel structure provides excellent resistance to slag penetration, protecting the underlying refractories.
Applications in High Temperature Kilns
Magnesia spinel bricks find extensive use in various parts of high-temperature kilns, including:
Furnace roofs: Due to their high melting point and resistance to slag erosion, they are commonly used to line the roofs of furnaces.
Sidewalls: The sidewalls of kilns, especially those exposed to high temperatures and corrosive environments, are often lined with magnesia spinel brick.
Hearth: The hearth of the kiln, which comes into direct contact with the molten material, can benefit from the wear resistance and slag resistance of magnesia spinel brick.
Regenerators: In regenerative kilns, magnesia spinel brick can be used to line the regenerator chambers.
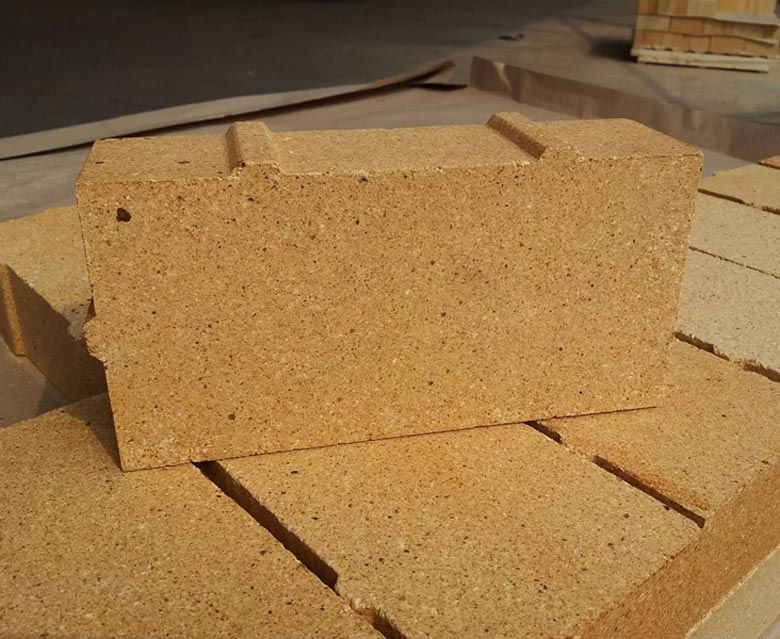
Advantages of Magnesia Spinel Bricks
Long service life: Magnesia spinel bricks offer a long service life, reducing the frequency of refractory replacement and maintenance.
Energy efficiency: Their excellent thermal insulation properties help to reduce heat loss, improving energy efficiency.
Improved product quality: The use of magnesia spinel bricks can help to improve the quality of the final product by minimizing contamination.
Reduced downtime: Their durability and resistance to wear and tear reduce downtime associated with refractory failure.
Conclusion
Magnesia spinel bricks are a critical component in high-temperature kilns, providing excellent performance in terms of thermal shock resistance, chemical resistance, and mechanical strength. Their unique properties make them an ideal choice for applications where high temperatures and corrosive environments are encountered. As industries continue to demand higher temperatures and more efficient processes, the importance of magnesia spinel refractory brick is likely to increase.
Comments