High Alumina Refractory Bricks for Hot Furnaces
- keruirefra
- 2024年9月30日
- 讀畢需時 6 分鐘
In high-temperature industrial applications, choosing the right refractory material is crucial to ensuring the efficiency, durability, and safety of the furnace. Among the various refractory materials available, high alumina refractory bricks are known for their excellent performance in extreme thermal conditions. These bricks, made primarily from alumina (Al₂O₃), are highly resistant to heat, chemical corrosion, and mechanical stress, making them a preferred choice for furnaces, kilns, and other high-temperature environments.
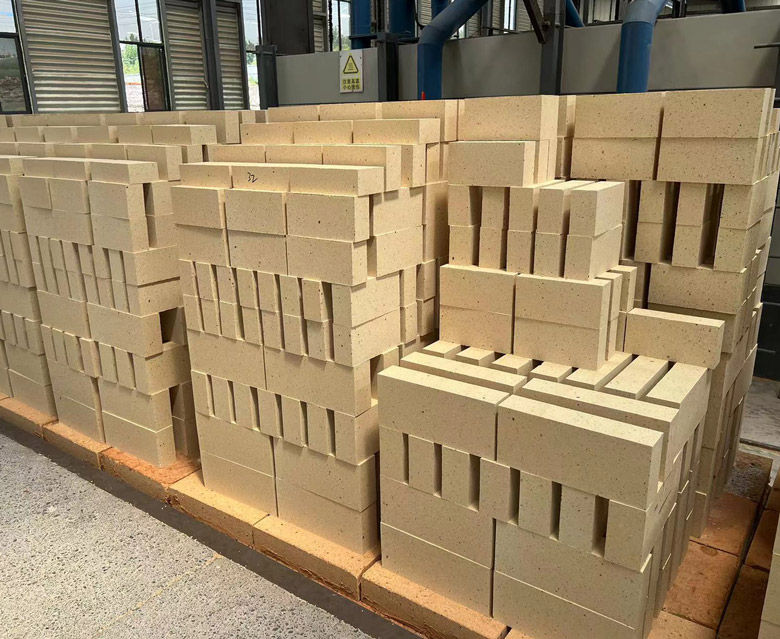
What Are High Alumina Refractory Bricks?
High alumina refractory bricks are a type of brick that contains a significant amount of alumina, generally between 45% to 99%. The higher the alumina content, the better the bricks can withstand high temperatures and corrosive environments. These bricks are typically composed of bauxite, kaolin, and other raw materials rich in alumina, which are sintered at high temperatures to form a dense, durable product.
High alumina bricks are divided into three categories based on their alumina content:
Class I Bricks: Contain between 45% and 60% alumina.
Class II Bricks: Contain between 60% and 80% alumina.
Class III Bricks: Contain more than 80% alumina, sometimes referred to as corundum bricks due to their high alumina content.
Properties of High Alumina Refractory Bricks
The properties of high alumina bricks make them ideal for use in high-temperature environments such as hot furnaces. Key properties include:
1. High Thermal Resistance
High alumina refractory bricks can withstand temperatures of up to 1800°C (3272°F), depending on their alumina content. This high resistance to heat makes them ideal for use in furnaces, kilns, and incinerators.
2. Low Porosity
Low porosity in high alumina bricks results in less permeability, which helps prevent the infiltration of gases, slags, and molten materials. This increases the durability of the bricks and improves their overall lifespan in harsh environments.
3. Excellent Mechanical Strength
High alumina bricks are known for their exceptional mechanical strength, allowing them to resist heavy loads and mechanical stress. This is particularly beneficial in furnaces that handle large amounts of raw materials, where structural integrity is critical.
4. Corrosion Resistance
High alumina bricks are resistant to chemical corrosion from slags, fluxes, and molten metals, making them suitable for use in industries such as metallurgy, cement production, and glass manufacturing, where such corrosive materials are common.
5. Thermal Shock Resistance
Thermal shock resistance is the ability of a material to withstand rapid temperature changes without cracking or losing structural integrity. High alumina bricks possess excellent thermal shock resistance, which is essential in environments where temperatures fluctuate frequently.
6. Wear Resistance
In high-wear environments such as hot furnaces, high alumina bricks show remarkable resistance to abrasion and erosion, ensuring a longer service life and reduced maintenance requirements.
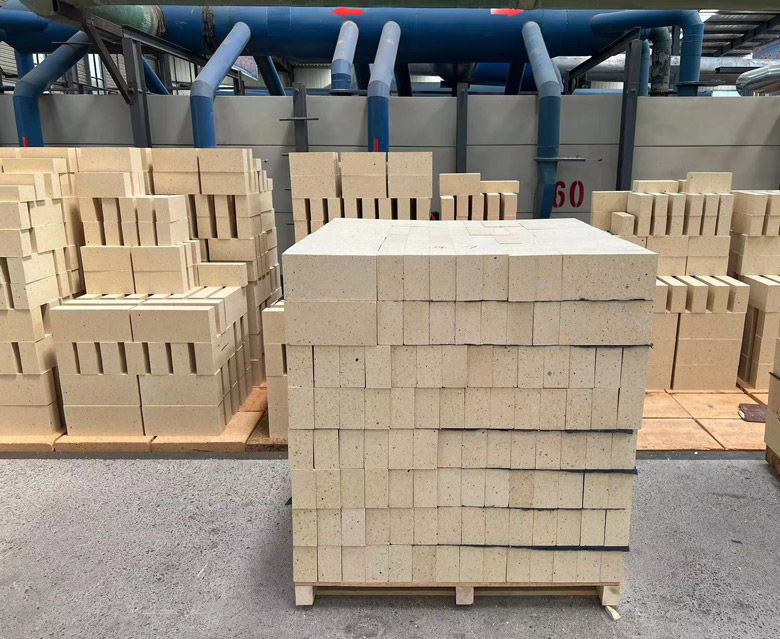
Applications of High Alumina Refractory Bricks in Hot Furnaces
Due to their unique properties, high alumina refractory bricks are widely used in various industries where high temperatures are required. Some key applications include:
1. Blast Furnaces
In the steelmaking industry, blast furnaces are used to extract iron from ore. High alumina bricks are often used to line the stack and hearth of these furnaces, as they can withstand the extreme temperatures and corrosive slag produced during the smelting process.
2. Hot Blast Stoves
Hot blast stoves, which preheat the air injected into blast furnaces, also utilize high alumina bricks. The high thermal resistance of these bricks ensures efficient heat retention and protection against thermal shock from the cyclical heating and cooling process.
3. Rotary Kilns
Rotary kilns, used in industries such as cement manufacturing and lime production, rely on high alumina refractory bricks to line their high-temperature zones. The bricks provide excellent resistance to the mechanical stresses and chemical corrosion caused by the raw materials and fuels used in the process.
4. Glass Furnaces
In glass production, high alumina bricks are used to line the melting tank, where raw materials are melted at high temperatures. The bricks' corrosion resistance and thermal stability help prevent contamination of the molten glass and prolong the lifespan of the furnace.
5. Incinerators
High alumina bricks are used in industrial waste incinerators, where temperatures are high, and corrosive byproducts can erode the refractory lining. The bricks' ability to withstand chemical attack and thermal cycling makes them ideal for use in these applications.
6. Electric Arc Furnaces (EAF)
Electric arc furnaces, widely used in steel production, operate at extremely high temperatures. High alumina bricks provide the necessary thermal resistance and structural integrity to withstand the intense heat and slag produced during steelmaking.
Benefits of High Alumina Refractory Bricks
Using high alumina refractory bricks in hot furnaces offers several significant advantages:
1. Enhanced Thermal Efficiency
High alumina bricks have low thermal conductivity, meaning they help retain heat within the furnace, reducing energy consumption and improving overall thermal efficiency.
2. Longer Furnace Lifespan
Thanks to their high thermal stability, corrosion resistance, and mechanical strength, high alumina bricks extend the operational lifespan of furnaces, reducing the need for frequent repairs and replacements.
3. Reduced Maintenance Costs
The durability of high alumina bricks reduces the frequency of furnace shutdowns for maintenance, saving time and money in industries where downtime can be costly.
4. Improved Product Quality
By providing consistent thermal conditions and resisting contamination from slags or molten materials, high alumina bricks help improve the quality of the materials being processed, whether it’s steel, glass, cement, or other products.
5. Versatility
High alumina bricks are available in various shapes, sizes, and alumina content levels, making them suitable for a wide range of furnace designs and applications.
6. Environmental Benefits
By improving the energy efficiency of furnaces and reducing fuel consumption, high alumina bricks contribute to a decrease in greenhouse gas emissions and the environmental impact of industrial processes.
Installation Considerations
Proper installation of high alumina bricks is critical to ensuring their performance in hot furnaces. Key considerations include:
1. Furnace Design
The choice of brick size, shape, and alumina content should be based on the specific design and operating conditions of the furnace. High alumina bricks may be combined with other refractory materials to achieve optimal thermal performance.
2. Installation Techniques
Skilled labor is required for the installation of high alumina bricks to ensure proper alignment and minimize gaps or voids in the lining. Poor installation can lead to heat loss, mechanical failure, and reduced brick lifespan.
3. Anchoring Systems
In some cases, high alumina bricks may be used in conjunction with metal anchoring systems to ensure stability during thermal cycling. These systems must be designed to accommodate the expansion and contraction of the bricks under high temperatures.
4. Thermal Expansion
High alumina bricks expand when exposed to high temperatures. Adequate spacing and allowances must be made to accommodate this expansion without compromising the structural integrity of the furnace.
Challenges and Limitations
While high alumina refractory bricks offer numerous benefits, there are some challenges and limitations associated with their use:
1. Cost
High alumina bricks tend to be more expensive than other types of refractory materials. However, the long-term benefits of durability, efficiency, and reduced maintenance can often offset the initial cost.
2. Brittleness
High alumina bricks can be more brittle than some other refractory materials, making them more susceptible to cracking under mechanical stress if not properly supported or installed.
3. Sensitivity to Thermal Cycling
While high alumina bricks are resistant to thermal shock, rapid or extreme temperature fluctuations over time can still cause degradation. Careful control of operating conditions is necessary to prevent premature brick failure.
Future Trends in High Alumina Refractories
As industries evolve, several trends are emerging in the use of high alumina refractory bricks:
1. Eco-Friendly Manufacturing
Manufacturers are increasingly focusing on producing high alumina bricks through environmentally friendly processes, such as using recycled materials and reducing emissions during brick production.
2. Nanotechnology
Research into nanotechnology is yielding high-performance refractory materials that can offer improved thermal resistance, strength, and flexibility, potentially enhancing the capabilities of high alumina bricks.
3. Smart Monitoring Systems
The integration of smart sensors and monitoring systems within furnace linings may provide real-time data on brick wear, temperature fluctuations, and thermal performance, allowing for predictive maintenance and optimization.
Conclusion
High alumina refractory bricks are indispensable in the construction and maintenance of hot furnaces used across various industries. Their exceptional thermal resistance, mechanical strength, and durability make them the material of choice for high-temperature applications. While they may come at a higher initial cost compared to other refractory materials, their long lifespan, reduced maintenance needs, and energy efficiency justify the investment. As technology advances, high alumina refractory bricks will continue to play a critical role in the optimization of industrial furnaces, enhancing both productivity and sustainability.
Rajasthan Lime & Minerals Pvt. Ltd. is a renowned name among calcined lime powder manufacturers in India, providing reliable solutions tailored to meet diverse industrial needs. A name you can trust