Different Types Of Magnesia Bricks For Different Kilns
- keruirefra
- 2024年9月19日
- 讀畢需時 5 分鐘
Magnesia bricks are a type of refractory material primarily composed of magnesium oxide (MgO). They are known for their high melting point and exceptional resistance to thermal shock, making them suitable for various high-temperature applications. This article explores the different types of magnesia bricks, their properties, manufacturing processes, and applications in various kilns.
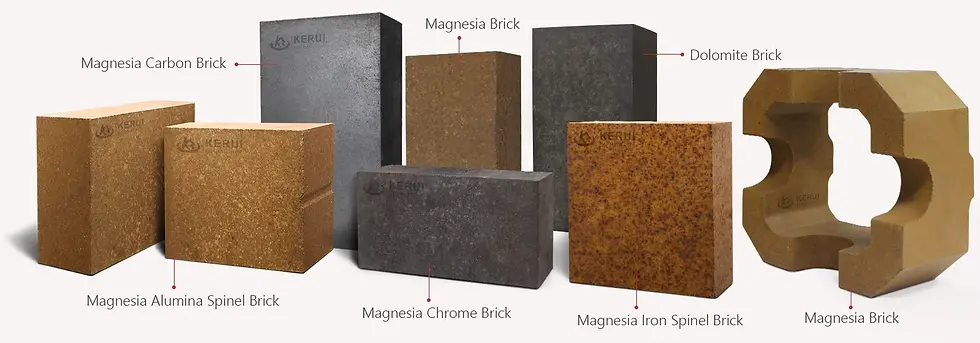
Overview of Magnesia Bricks
Magnesia bricks are widely used in industries that require materials capable of withstanding extreme temperatures and harsh chemical environments. The primary component, magnesium oxide, can be derived from natural magnesite or produced synthetically. Depending on the production process, magnesia bricks can be categorized into two main types: burned magnesia bricks and chemically bonded magnesia bricks. This web offers more information about bricks for you: https://keruirefra.com/magnesia-refractory-brick/.
1. Burned Magnesia Bricks
Burned magnesia bricks are produced by firing raw magnesite at high temperatures (around 1500-1800°C). This process results in a dense and strong refractory material with high refractoriness and excellent resistance to alkaline slags. Common types of burned magnesia bricks include:
High-Purity Magnesia Bricks: These contain over 97% MgO and are used in applications requiring high thermal stability and resistance to corrosion. They are ideal for use in electric arc furnaces and steelmaking processes.
Magnesia-Alumina Bricks: These bricks combine magnesium oxide with alumina (Al2O3) to enhance mechanical strength and thermal stability. They are often used in applications where both acidic and basic conditions exist.
Magnesia-Chrome Bricks: Made by combining magnesia with chromium oxide (Cr2O3), these bricks exhibit excellent thermal shock resistance and are commonly used in steelmaking converters and ladles.
Magnesia-Calcium Bricks: These bricks incorporate calcium oxide (CaO) to improve performance in specific environments, such as lime kilns.
2. Chemically Bonded Magnesia Bricks
Chemically bonded magnesia bricks, also known as unburned magnesia bricks, are produced by mixing raw materials at room temperature without firing. This type of brick offers good mechanical performance and alkali resistance. Common types include:
Magnesia Carbon Bricks: These bricks combine magnesium oxide with carbon materials such as graphite. They provide excellent thermal conductivity and resistance to oxidation, making them suitable for use in steelmaking furnaces.
Alumina-Magnesia Carbon Bricks: Similar to magnesia carbon bricks but with added alumina, these bricks offer improved thermal stability and mechanical strength.
Magnesia-Calcium Carbon Bricks: These incorporate calcium carbonate along with magnesium oxide, enhancing performance in specific applications like rotary kilns.
Properties of Magnesia Bricks
Magnesia bricks possess several key properties that make them suitable for high-temperature applications:
High Refractoriness: With melting points exceeding 2800°C, magnesia bricks can withstand extreme temperatures without losing structural integrity.
Thermal Shock Resistance: Their ability to endure rapid temperature changes without cracking is crucial for applications where thermal cycling occurs frequently.
Chemical Resistance: Magnesia bricks exhibit strong resistance to alkaline slags and other corrosive materials, making them ideal for use in environments where chemical attack is a concern.
High Density: The density of magnesia bricks contributes to their durability and ability to resist wear in abrasive conditions.
Moderate Thermal Expansion: This property helps maintain dimensional stability during heating and cooling cycles.
Manufacturing Process
The manufacturing of magnesia bricks involves several steps:
Raw Material Selection: High-purity magnesite is chosen as the primary raw material. The quality of the raw material significantly impacts the performance of the final product.
Mixing: For chemically bonded bricks, raw materials are mixed with binders at room temperature. In contrast, burned magnesia bricks undergo high-temperature firing after mixing.
Molding: The mixed materials are pressed into molds to form the desired brick shapes. This step is crucial for achieving uniform density and dimensions.
Drying: The molded bricks are dried to remove moisture content, which helps prevent cracking during firing or hardening.
Firing: For burned magnesia bricks, the dried products are fired at high temperatures to enhance their properties. Chemically bonded bricks may not require this step but may undergo curing processes instead.
Cooling: After firing, the bricks are cooled gradually to avoid thermal shock.
Quality Control: Rigorous testing is performed on finished products to ensure they meet specific standards for density, strength, porosity, and thermal performance.
Applications of Magnesia Bricks
Magnesia bricks find extensive use across various industries due to their exceptional properties:
1. Steel Industry
In the steel industry, magnesia bricks are used extensively due to their ability to withstand high temperatures and corrosive environments:
Electric Arc Furnaces (EAF): High-purity magnesia bricks line EAFs where molten steel is produced.
Basic Oxygen Furnaces (BOF): Magnesia-chrome or alumina-magnesia carbon bricks provide durability against slag erosion.
Ladles: Magnesia-carbon bricks help maintain temperature during metal transfer processes.
2. Non-Ferrous Metal Industry
In non-ferrous metal production, such as copper or aluminum smelting:
Smelting Furnaces: Magnesite-chrome or chemically bonded magnesia bricks line smelting furnaces due to their chemical resistance against non-ferrous metal slags.
Refining Processes: Magnesia-carbon bricks are utilized for their thermal stability during refining operations.
3. Glass Industry
In glass manufacturing:
Glass Melting Tanks: High-purity magnesite refractories line glass melting tanks due to their ability to withstand high temperatures without reacting with molten glass.
Regenerative Furnaces: Magnesite-alumina or carbon-bonded types provide durability against thermal cycling and chemical attack from glass materials.
4. Cement Industry
In cement production:
Rotary Kilns: Magnesite refractories line rotary kilns where limestone is calcined at high temperatures.
Preheaters: Chemically bonded magnesite brick types offer good insulation properties while resisting wear from raw materials.
5. Ceramics Industry
In ceramics manufacturing:
Kilns: High-purity magnesite refractories provide insulation and structural support in kilns used for firing ceramics at elevated temperatures.
6. Incineration Systems
In waste management:
Incinerators: Magnesite refractories withstand the harsh conditions present in incinerators while resisting slag erosion from burning waste materials.

Advantages of Magnesia Bricks
Using magnesia bricks offers several advantages over other refractory materials:
Longevity: Their durability leads to extended service life compared to traditional refractory materials, reducing maintenance costs over time.
Cost Efficiency: Although initial costs may be higher than some alternatives, reduced replacement frequency can result in overall cost savings.
Environmental Sustainability: The production processes can be optimized for sustainability, contributing positively to eco-friendly industrial practices.
Energy Efficiency: Their low thermal conductivity helps maintain internal temperatures within kilns or furnaces while minimizing energy loss.
Conclusion
Magnesia bricks play an essential role in various high-temperature industrial applications due to their superior properties such as high refractoriness, excellent thermal shock resistance, and strong chemical resistance. With different types tailored for specific uses—from burned magnesia bricks suitable for steelmaking furnaces to chemically bonded varieties ideal for non-ferrous metal production—these refractory materials enhance operational efficiency across multiple sectors including steelmaking, glass manufacturing, cement production, ceramics processing, and waste incineration systems. As industries continue seeking reliable solutions for extreme conditions, the demand for high-quality magnesia refractory products will likely grow, further solidifying their importance in modern industrial processes.
Comments