Applications of Kerui Magnesia Carbon Refractory Brick
- keruirefra
- 2024年10月14日
- 讀畢需時 6 分鐘
Magnesia carbon refractory bricks, also known as magnesia-carbon bricks (MgO-C bricks), are a widely used refractory material in high-temperature industries, particularly in the steelmaking industry. These bricks combine the properties of two materials—magnesia (MgO) and carbon (C)—to offer excellent resistance to thermal shock, slag corrosion, and oxidation, making them ideal for use in the harsh conditions of steel furnaces, ladles, and converters.
In this comprehensive article, we will explore the key properties of magnesia carbon bricks, the manufacturing process, and the critical applications where these bricks are indispensable. Additionally, we will discuss the factors influencing the performance of magnesia carbon bricks and their future development in the refractory industry.
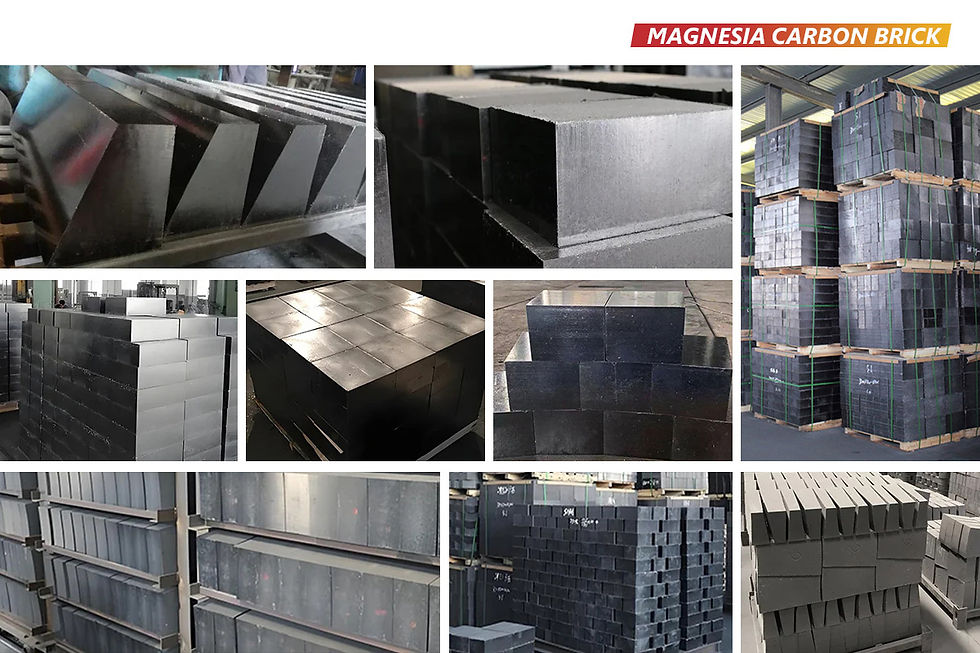
Composition and Properties of Magnesia Carbon Bricks
Magnesia carbon bricks are made from a combination of high-purity magnesia (MgO) and carbon-based materials, typically in the form of graphite. These two materials are bonded together using pitch, resin, or other organic binders. The specific ratio of magnesia to carbon varies depending on the intended application, but typically, magnesia accounts for 70% to 95% of the brick's composition, while carbon makes up 5% to 30%.
The exceptional properties of magnesia carbon bricks are due to the synergy between magnesia and carbon, each contributing distinct characteristics:
1. Magnesia (MgO)
High Refractoriness: Magnesia has a high melting point of around 2,800°C (5,072°F), giving the brick excellent resistance to high temperatures.
Chemical Stability: Magnesia is chemically stable in basic (alkaline) environments, making it highly resistant to corrosion by basic slags and other alkaline compounds.
Mechanical Strength: Magnesia contributes to the brick's mechanical strength, making it capable of withstanding heavy loads and impacts.
2. Carbon (Graphite)
Thermal Shock Resistance: Carbon, especially in the form of graphite, imparts excellent thermal shock resistance to the brick. It can absorb the stresses caused by rapid temperature changes, preventing cracking or spalling.
Non-Wetting Properties: Carbon is non-wetting to molten slag and metals, which helps to prevent slag infiltration and corrosion of the brick.
Oxidation Resistance: The addition of antioxidants (such as aluminum, silicon, or magnesium) helps improve the carbon’s oxidation resistance at high temperatures.
3. Other Additives
Antioxidants: To enhance the oxidation resistance of magnesia carbon bricks, various antioxidants like aluminum (Al), silicon (Si), and magnesium (Mg) are added to the mixture. These additives react with oxygen and prevent the oxidation of the carbon content, thus extending the brick's lifespan.
Key Properties of Magnesia Carbon Bricks
High Refractoriness: Magnesia carbon bricks have a high melting point and can withstand extremely high temperatures, often exceeding 1,600°C (2,912°F).
Excellent Thermal Shock Resistance: The graphite content gives the bricks outstanding resistance to rapid temperature changes, making them suitable for applications involving frequent heating and cooling cycles.
High Corrosion Resistance: The combination of magnesia and carbon provides excellent resistance to chemical corrosion, especially by basic slags in steelmaking processes.
Good Mechanical Strength: Magnesia carbon bricks are highly durable and can withstand the mechanical stresses typically encountered in furnaces and converters.
Oxidation Resistance: With the addition of antioxidants, these bricks offer improved resistance to carbon oxidation at high temperatures, prolonging their service life.

Manufacturing Process of Magnesia Carbon Bricks
The manufacturing process of magnesia carbon bricks involves several steps, each contributing to the final product's performance and durability. Below is a detailed overview of the key stages in the production process:
1. Raw Material Selection
The quality of the raw materials used in magnesia carbon brick manufacturing directly impacts the brick's performance. The primary raw materials include:
High-Purity Magnesia: Magnesia used in the production of magnesia carbon bricks is typically derived from natural magnesite or seawater. High-purity magnesia (with an MgO content of 95% or higher) is essential to achieve the desired refractoriness and corrosion resistance.
Graphite: Flake graphite is the most commonly used form of carbon in magnesia carbon bricks due to its excellent thermal conductivity and oxidation resistance.
Binders: Organic binders such as phenolic resin, pitch, or asphalt are used to bond the magnesia and graphite particles together.
Antioxidants: Additives like aluminum, silicon, and magnesium are incorporated into the mixture to enhance the oxidation resistance of the carbon content.
2. Mixing
Once the raw materials are selected, they are carefully mixed together to ensure a uniform distribution of magnesia, graphite, and binders. The mixing process is critical to achieving the desired consistency and workability of the material. Precise control of the mixing time and temperature is essential to prevent agglomeration and ensure proper bonding between the magnesia and graphite particles.
3. Shaping (Forming the Bricks)
After mixing, the material is shaped into bricks using one of the following methods:
Dry Pressing: The mixture is placed into a mold, and hydraulic or mechanical presses apply high pressure to compact the material into the desired brick shape. Dry pressing is the most common method for producing magnesia carbon bricks due to its ability to create dense, uniform bricks with excellent mechanical properties.
Isostatic Pressing: In this method, the material is pressed uniformly from all directions using hydraulic pressure. Isostatic pressing is often used to produce bricks with complex shapes or for applications requiring exceptionally high strength and density.
After shaping, the bricks are left to dry at low temperatures to remove excess moisture and harden the binder.
4. Curing and Heat Treatment
The shaped bricks undergo a curing process in which the organic binder is polymerized at temperatures around 200°C to 300°C. This heat treatment ensures that the binder sets and solidifies, binding the magnesia and graphite particles together. Curing is essential for imparting the necessary strength and durability to the bricks.
5. Final Quality Control and Testing
After curing, the bricks undergo rigorous quality control testing to ensure they meet the required specifications. Key tests include:
Dimensional Accuracy: Ensuring that the bricks meet the required size and shape tolerances.
Bulk Density: Measuring the density of the bricks, which correlates with their mechanical strength and durability.
Cold Crushing Strength: Testing the mechanical strength of the bricks by applying pressure until they break.
Thermal Shock Resistance: Evaluating the brick's ability to resist cracking or spalling when exposed to rapid temperature changes.
Refractoriness Under Load (RUL): Measuring the brick's ability to maintain its shape and strength under high temperatures and mechanical loads.
Only bricks that pass these stringent quality control tests are approved for use in high-temperature industrial applications.
Applications of Magnesia Carbon Bricks
Magnesia carbon bricks are primarily used in industries that operate at extremely high temperatures and involve exposure to corrosive slags and gases. Some of the key applications of magnesia carbon bricks include:
1. Steelmaking Industry
Magnesia carbon bricks are widely used in the steelmaking industry, particularly in basic oxygen furnaces (BOFs), electric arc furnaces (EAFs), and ladles. In these applications, the bricks are exposed to high temperatures, mechanical stresses, and corrosive slags. The excellent thermal shock resistance and corrosion resistance of magnesia carbon bricks make them ideal for lining the critical areas of steel furnaces, such as:
Furnace Lining: Magnesia carbon bricks are commonly used to line the interior of basic oxygen furnaces and electric arc furnaces, where they withstand extreme temperatures and slag corrosion during the steelmaking process.
Ladle Linings: In steel ladles, where molten steel is transported and processed, magnesia carbon bricks provide the necessary durability and resistance to thermal cycling and slag infiltration.
Tapholes and Slag Lines: These bricks are also used in the slag lines and taphole areas of steel furnaces, where they must endure high temperatures and mechanical wear.
2. Non-Ferrous Metal Industry
Magnesia carbon bricks are used in the non-ferrous metal industry for lining furnaces involved in the production of copper, aluminum, and other non-ferrous metals. These furnaces require materials with high refractoriness and resistance to chemical attack by slags and molten metals. Magnesia carbon bricks offer excellent performance in these demanding environments.
3. Cement Industry
In the cement industry, magnesia carbon bricks are used to line rotary kilns, particularly in the transition and burning zones where the bricks must withstand high temperatures and the corrosive effects of cement clinker. Their ability to resist chemical corrosion and thermal shock makes them ideal for this application.
4. Glass Industry
Magnesia carbon bricks are also used in glass melting furnaces, where they provide excellent resistance to corrosion by molten glass and high temperatures. These bricks are particularly useful in the superstructure and regenerator sections of glass furnaces.
Looking for premium-quality calcined lime powder manufacturers in India? Rajasthan Lime & Minerals Pvt. Ltd. ensures consistent quality and customer satisfaction with every product